■ オンロード

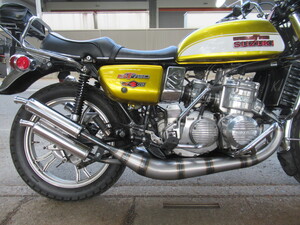
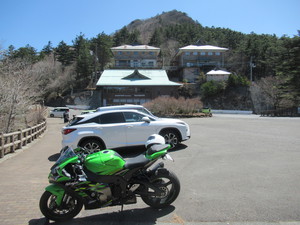
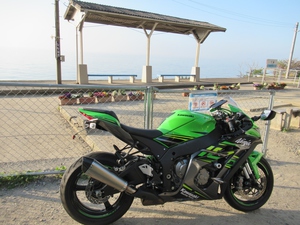
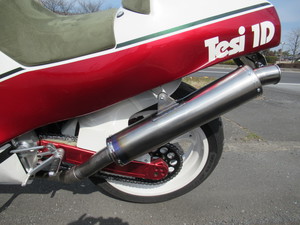
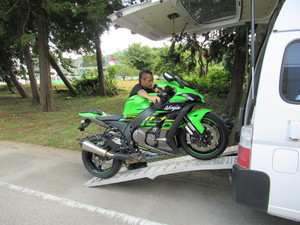
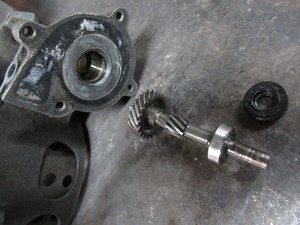
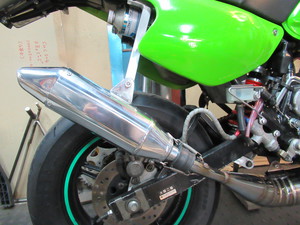
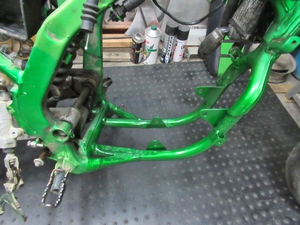
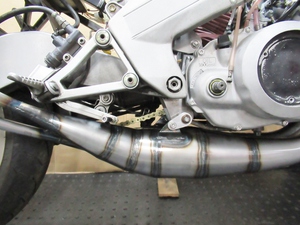
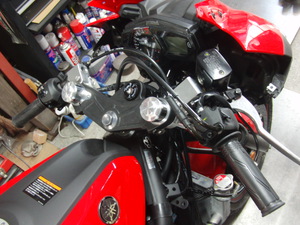
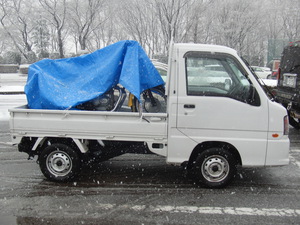
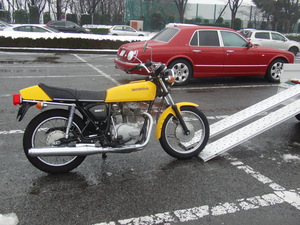
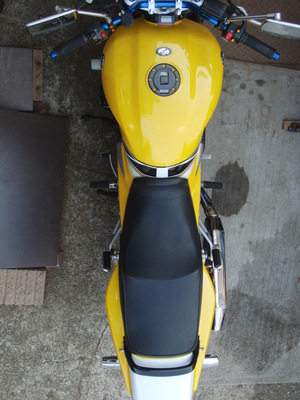
今週はドリーム50のアルミタンク製作です。お預かりして5ヶ月くらい経過していますので、お客さんも待ちくたびれているかもしれません。
依頼内容はRC116のような形のタンクにしたい、ということです。
実車はホンダコレクションホールにあるのですが、2月末まで館内改装のため休館です。
仕方なく画像を見ながら作ってみることにします。
しかし、驚くほど細長いタンクです。
作り始めてみますと、RC116とドリーム50はフレームのレイアウトが全然違うことに気がつきました。
おそらく、ドリーム50はサーキット走行だけでなくツーリングに使っても支障ないようにシート幅が広くなっています。そのためシートレールも幅広ですから、こちらのフレームに合わせたタンク形状にしないと取りつけが困難なことがわかりました。
画像は底板の上にタンク上部と横板を仮止めして形状確認を行っています。
板金で成形したアルミ板を溶接で繋ぎます。
外側の溶接ビードは研磨して消しますので内側の溶接をしっかりとつけておきます。
明日外側の溶接作業にかかります。
かなり進行しているように見えますが、完成まであと3日くらいかかるでしょう。
普通のタンクはメインパイプの上まで被さっていますが、このタンクはシートレールの上まで伸びていますので、トンネルの形状が複雑になります。
2枚の隔壁はガソリンの移動を抑える目的とタンクの剛性を上げる目的があります。
RC116はワークスマシンですが、ドリーム50は市販レーサーCR110に似せて製造されたマシンですからフレームの構成が違うわけです。
ガソリン溜まりにコックを取り付けますが
本体への溶接は研磨後にします。
突起物が無い状態の方が取り扱いしやすいためです。
RS125から移植するタンクキャップも同様です。
溶接はひととおり終わり、接合部の研磨と表面の均しを大雑把に行いました。
タンク容量は7.0Lです。ノーマルの容量は知りませんが、DE耐とか走るようでしたら気になるところですね。
ノーマルはCDIユニットがシートレールの上にはみ出しているため取り付け位置を変更してタンク底板をフラットにしてあります。
前下がりだったノーマルタンクはガソリンが前方に残ってしまい最後まで使いきらないらしいですが、このタンクは水平になっていますのでガソリンを使いきれるでしょう。(給油量を制限される耐久レースでは有効です)
ニーグリップ部分はシートレールより狭くなっています。RC116はもっと狭いですが、フレームとのマッチングでこれくらいが狭さ限度でしょう。
本来は赤色塗装ですが、お客さんの要望でアルミ地肌で終了です。
お客さん独自のプロジェクトがある限り私の業務も続いていくでしょう。
仕上げにサンドペーパーで磨きました。ハンマー痕や溶接ビードなどで表面の細かな歪みを平滑に均していきます。
60番から磨きはじめて180番で止めておきました。鏡面に仕上げるよりこれくらいの粗さの方が塗装の密着はいいでしょう。さらに磨きこんでポリッシュすることも可能ですが、あとはオーナーに委ねます。
ホンダはHSV010でGT500に挑戦しているというのに、このプロジェクトは何とささやかなものか。
全部手仕上げですからね、ハイテク一切無し!
カーレースの方はホンダのお家芸だと思うのですが、GT500では苦戦を強いられているようです。
技術力だけでは負けないと思うのですがそれだけじゃないんですね。
F1よりこっちの方が道路で乗れるクルマに近いので好きですね。絶対乗れないわけですけど、少年時代のスーパーカーブームを彷彿させます。
もてぎ貸切で極秘テストですかー
金持ちのレーシングチームは違いますね。というより、サーキットも自社所有でした。
研究所もテストコースも部品メーカーもなんでも揃っているのに何故、勝てないのか!
今年こそはレーシングスピリッツ見せてもらいましょう。
しかし、この顔 強そうやな。
ようやく2台目のNSR250のチャンバー作りです。製作実績がありませんので、毎回悩むところですが、今回はお客さんの要望で右二本出しのサイレンサーが特徴です。
89モデルと思われますが外装部品は既に廃盤になっています。フルカウルは全塗装したのかと思っていましたが、じつはグラスファイバーで復刻したものでした。
ノーマルはインジェクション成型なので、裏地の肌が違うことで気がつきましたが、生産されない旧車のために、カウリングを少量生産するメーカーがあるようです。
引き締まったスタイリングが好感をもてますね。
アンダーカウル装着のためにチャンバーの取り回しが複雑になります。
90度V型のリヤバンクは右出しに、フロントバンクはUターンして左出しという変則カーブを描きます。
通常左向きにひねったコンバージェントコーンを右向きに変更して右出しのテールパイプに繋げています。元々センタースタンドが無く、リヤサスのリンク位置も問題なく、後ろ側の取り回しは自然な形にできました。
まだまだ年内はワンオフの製作が続きます。当分の間、工房に篭って仕事していますので春ころまで掛かります。電話も出られないと思いますがご了承ください。
息抜きは必要なので、今日の音楽ネタはコテコテのジャズにロックを融合させて聴きやすい音楽を作ったフュージョン界の功労者、デイブ・グルーシンの立ち上げた演奏集団GRP AllStarsからマウントダンスです。自分はデイブ・グルーシンの演奏を観るのはこれが始めてで感動しました。ギターの神様リー・リトナーも参加されています。この楽曲聴いていると80年代が蘇ってきます。
NSR250R 89モデルです。これはチャンバー製作のためお客さんに持ち込んでいただいたものですが、私が会社員時代に新車で購入して乗っていました。
2年ほど通勤やツーリングで使用しましたが出張が多くなり、オートバイとも不縁になりがちで段々乗らなくなり手放してしまいました。
あれから25年も経つのに、このように綺麗に保存されている人がいることに感心します。
買いなおそうと思っても、この年式は高額になっていることと、純正部品も絶販が多くなってきていますので止めておきます。チャンバー製作記は後日(1ヶ月ほど)掲載することにして
今回の題材はこれです。
純正のサイレンサーですが、この何気ない部品に非常に高度な鍛造技術が使われています。
このボルト締めのフランジ部分と筒が一体成型であること、この製法が想像できるでしょうか。私は別の部品製造の打ち合わせで某鍛造メーカーへ出張したときに、この部品を見つけました。ホンダが発注するサイレンサーのメーカーは別にあるのですが、その会社から手配された2次メーカーだということです。
一般的には認知される企業ではありませんが鍛造専門として自動車工業界を支えている重要なスポットにあると思います。当時の打ち合わせの目的は、設計からは図面が出され、購買部でメーカーを選定して発注する、製作所では部品を受け入れて組み立てる。という自動車製造の流れの中で部品メーカーと受け入れ側の取り決めを行っていないと、担当が別々の人間が行っているので勝手に作られると量産が成り立たなくなるためです。
搬入の何週間前に発注するとか、ロットの大きさ(一回に製造する数)などは購買で取り決めします。私の担当は受け入れる部品に不良が混入しないための取り決めです。不良の検出は検査によって行いますが、製造工程で不具合を出さないことが重要で、そのための重点管理項目はどのようになっているか、現場ではどのように行っているか、実際に確認する必要があります。
そんな製造現場で見てきたものの中にこのサイレンサーのような一体成型があったわけですが、特殊な金型と大型のプレス機を使って、ビレット(仕込み重量と形状を管理された材料)を金型に押し込み、筒の部分は金型の隙間を滑りながら伸びてくるという、想像を絶する塑性変形を伴います。
通常は冷間で行うようですが、このような変形抵抗の大きいワーク(製作物)は必要におうじて加熱炉で温めて柔らかくしてから鍛造します。ここで、非常に高荷重で金型と材料が滑って変形していきますので金型と材料には特殊な潤滑材も塗布されています。
普通の鍛造はワークの型抜けを考えて「抜け勾配」がついているものですが、これは抜け勾配ゼロなのです。押し出し成型に近い製法であることが伺えます。
これがエンドキャップ部分ですがフランジを内側カーリングで荷締めて固定されています。
これで非分解部品となるわけですが、ここまでの工程でサイレンサー外筒部分にフランジのタッピング以外に加工はありません。
全て金型と専用機で成型しますので人間の手作業はワークの運搬だけということになります。
品質は工程で作られるもの、人為的なミスや熟練の度合いで製品がバラつくことを防ぐということが量産の考え方でした。
なにしろ切削加工なしでサイレンサーが出来てしまいますので、無駄がありません。こういうことを業界用語で「歩留まりがよい」といいます。厳密にコストが算出され、安価に提供せよという親会社からの要求に応えた形ではないかと思います。
今の私の仕事は全く逆のことをやっています。量産はできないので、一個だけ作る人為的技術が製品の可否を左右します。おそらく量産を経験していないと、こういう発想も起こらなかったでしょう。
世間は大型連休中ですが、予定の業務が終了していない弊社はエンドレスで進行中です。
1ヶ月近くお預かりしているマシンのチャンバー製作に着手しているところですが、予想に反して手強いです。
TZR250の後期モデル、89年から3年しか生産されなかった前方吸気、後方排気という珍しいレイアウトのエンジン。
91年からV型となるため並列2気筒としては最後のモデルとなります。
しかし、このレイアウトはメリットとデメリットがあって総合的にはどうなのか、いろいろ乗り込んだ人しか分らないと思いますが、私個人的には面白いですね。
何で他の機種ではこういうレイアウトが採用されなかったのか興味深いところがあります。
クランクケース吸入ですから、キャブレターが後ろでも前でも吸気量は同じですが、通常レイアウトではキャブレター周りが熱くなってしまいますが、前方なら冷やされますから、フレッシュなエアーが吸入され充填効率が上げられるでしょう。排気管も後ろ向きの排気ポートからストレートに排気され抵抗も少ないでしょう。
チャンバーの寸法は依頼者からエクセルで作図したものをメール送信していただき、それに従って製作するだけです。ところが、真っ直ぐなパイプを作るわけではありませんので微妙なカーブを作ることで難航しています。
左右のエキパイを成型して口元フランジを固定してみると、これではパイプの位置が高すぎます。シートの下が近くて配線などが焼けてしまうことになりそうなので、やり直しです。ここまで2日かかっていますが、惜しげもなく廃却です。
即効で少し下向きに変えたカーブのエキパイ2本を作成して続行です。
このようなことを繰り返していますので予定どおり業務が進まないということになります。
納期は約束しても無駄ということです。
初めて作るものはどうしても時間がかかりますが完成したときの喜びも既成品とは違うものがあるのです。
うーむ、官能的です。
リヤストレートとは名ばかりで、クネクネ曲がってないと、サブフレームやサイドカバーと干渉してしまうので、必然的なカーブを描いています。
これからテールパイプとサイレンサー2本作らなければ完成しません。
あと20時間くらいでしょうか、もうひと頑張りします。
サイレンサー2本、リヤカウルに空いた穴から突き出しています。
4ストのセンター出しは、このモデルから発展したと言えます。センターはリヤタイヤが上がってきますので、チャンバーは両側に張り出した形状にしないと当たります。
サイドカバー付けると全部隠れて見えなくなりますのでストリップ状態だとこのようになります。
これでオーナーの設計されたチャンバースペックで製作が完了しました。
GW+3日の工程費やしましたので、この後も過密スケジュールで進行していきます。
ダイノジェット計測でお世話になっているmotoGLADさんとこのテイスト仕様のロードレーサーです。
チャンバーのワンオフ製作をやる予定ですが、今月中の納期なのに今頃取りかかっていて大丈夫なのでしょうか。
社外品のチャンバーが付いていましたが、満足できず新作してほしいという依頼で、内容を確認しますと、中速の加速が緩く、高回転も頭打ちが早い。サーキット走行では少々物足らないと感じるようです。
チャンバースペックを測ってみましたら、どうやらストリート向けで強烈なパワー特性を控えたおとなしい乗り味になっている様子です。
幸い弊社では17年かけて溜め込んだチャンバースペックが多数、秘蔵ノートに書き込んでありますので、これは2ストパラレルツインの250ccなので125シングルエンジンのレーサースペックを引用して製作していきたいと考えています。
それから形状デザインですが、付いていたチャンバーはエキパイがクロスしたタイプでしたが、右バンクで路面とヒットしてしまうのでレイアウトを見直す必要があります。当然左右非対称となりますので、違う型を2種類作ることになります。筑波サーキットは右の高速コーナーが多いので右バンクの条件が厳しくなってしまうのです。
ではこれから1週間はこれに専念することになりますので、他の仕事は一切できません。戦闘機向けのチャンバー製作は最も意欲的な作業であります。
チャンバー形状を見直す工程ですが、膨張部分が後ろに位置すると、リヤサスのリンクと干渉するため外側に張り出してしまいます。フレームから僅かにはみ出した部分がフルバンクしたとき、路面と擦ってしまうので
膨張部分を完全にフレームの下に収めるレイアウトを取らなければなりません。
そのためエキパイ部分をなるべく前方に取りまわすために、このようなクロス形状にしてみました。膨張部分とダイバーコーンは左右別形状になりますので、このあと展開図を作成していきます。
右側のチャンバーは、このとおり繋がりました。膨張室を完全にエンジン下部へ追い込んであります。
次に左側のチャンバー形状を決めます。
左側はこんな形状です。チャンバーのスペックは左右同じなのですが微妙に形状を変えないと、フレーム下にピッタリと収まりません。もうガチガチのクリアランスで5mm動かすとフレームやステップブラケットと干渉しますが、これでフルバンクでも路面と接触することはないでしょう。
あとはマウントステーとテールパイプを溶接してサイレンサーを取りつけます。
取りつけ確認して完成です。
サイレンサーは125ccシングルの標準的なサイズです。サイレンサーマウントはありませんのでテールパイプ溶接部に補強パッチを当てて亀裂防止してあります。
motoGLADさんはロードレース経験豊富なので、キャブセッティング、パワーチェックなどお任せしたいと思います。
チャンバーは未塗装です。運転中の排気熱で焼けてしまえば、錆びの進行が遅くなりますので問題ないですが、長時間保管する場合は防錆スプレーか耐熱塗装がよいでしょう。
NSR50のロードレーサーが今回の議題。
GPmonoでレースをされているナオキさんの練習車ですが、ミニバイクは転倒も多いそうでダウンチャンバーだと、サイレンサーは路面に擦ってしまうため
サイレンサーをリヤカウルの中を通す、センター出しに改造するためチャンバーをアップタイプに変更してフレームの中を通すレイアウトに作り変えるというもの。
チャンバーを作るとき、最初にやることは元になるチャンバーの寸法を測ってストレート図に書き直すことです。
写真の上側は元のチャンバー
下側はストレート図に基づいて作られた模型
円盤はパイプの内径を表し、軸芯の棒はパイプの長さを表します。
この模型を曲げて車体に取り回すレイアウトを検討します。
このようにエンジンやフレームとの隙間を確認しながら形状を決めていきます。
同じものは二度と作りません。この車両だけのためのワンオフ製作です。
このあとアンダーカウルやキャブレターの燃料ホースなどに当たらないようにクネクネと複雑なカーブを描いて、狭いフレームの隙間にチャンバーが収まっていきます。
明日は模型の形状に合わせてパイプを成型していきます。
成型されたパイプを接合しました。
模型のカーブに似ていますが、車体がアップチャンバーを想定して設計されていないために取り回しはミリ単位でフレームをかわすシビアなものになりました。
アンダーカウル装着のため、フレームギリギリに寄せないと、グラスファイバーのカウルを溶かしてしまうことになります。
明日はラジエターのマウントとセンター出しサイレンサーのフィッティングを行います。
震災の前日から製作に取り掛かっていたタンク作りですが、3日ほど動揺して通常の業務ができませんでした。とりあえず、やりかけた仕事を完了させるべく再開しましたが、計画停電で一日のうち3時間くらいは業務中断になってしまい、非常に効率悪いです。
被災地の電力不足、燃料供給不足を考え、工場の空調や石油ストーブを止めてやっております。幸い寒冷地ではないので、寒いですが我慢しながら仕事しています。これも支援の一つと考えております。
義援金や救援物資だけが災害支援ではありません。最も強力な支援は国の力だと思うのです。自衛隊や消防庁に指令を出したり、車両を動かしたり、職員の人件費を払ったり、全て税金でまかなうのですから被災していない地域の人ができる最も重要なことは、今やっている事業をしっかりと遂行して税金を払うということであると思っています。
アルミ板金でこしらえたガソリンタンク。
オーナーさんはジムカーナでNSR250に乗っていますが、ノーマルタンクの張り出しが大きいことと、エアクリーナー吸気口を塞いだデザインを改善するという目的でタンク製作に踏み切りました。
フィラーキャップはノーマルを使用していますので鍵を使って開閉します。
タンク底板の形状です。エアクリーナーボックスを逃がすデザインです。
中央付近に二つ穴が設けていますが、フィラーキャップの構造上、エアベントと水抜きのパイプがタンク内部を貫通しています。
車体に装着した様子です。
フューエルコックは左下に設置してあります。
レーサー用の部品で、リザーブ無しです。
タンク容量は13L、大体これでご要望にお答えできると思います。
停電や燃料の調達が悪く通常より効率悪いですが、まだまだバックオーダー抱えておりますので、なるべく早く仕事を進めていくだけです。
そのお客さんは始め電話で場所を確認してからスポーツカー(ロータス)に乗って現れました。
怪しげな工場の下見をしてから注文しようと考えたそうです。
以前、別の業者に品物を注文したがトラブルになってしまい信用できなくなったらしく、製作を依頼するとき慎重にならざるを得なくなったそうです。
それなら大丈夫、信念の仕事をやり通す弊社を選んだあなたは大正解。
必ずや満足させてあげられるでしょう。
最初、装着されていたチャンバーも社外品だったのですが年式も古く錆びている上に素人のような溶接が割れてしまって何度も下手な補修を重ねた痕が見られました。
もちろん修理ではなく新品製作で排気漏れも解消、パワーモリモリのチャンバーがついたRD400がロータスのおじさんの通勤車として走り続けているそうです。