■ プロダクツ
安易に引き受けてしまって、またもや後悔の念に苛まれていますが、引き受けるに至った理由の一つに必要条件がなかったことが挙げられます。コストも制限されていませんし、サーキット走行目的なので音量や排ガスの規制もありません。作り手としては全く自由な要件なので、引き受けやすかったのです。取り掛かるまで日数も長かったので、やり始めてから考えればよかろうと思っておりました。
L型ツインのリヤバンクは後方排気でエキパイ長が極端に短いのです。
ノーマルはマフラーというより箱型チャンバーです。後方排気の容積をチャンバー内の隔壁で距離をかせいで確保していると思われます。
触媒はフロントバンクのエキパイの途中とリヤバンク用はチャンバー内に装着されているのですが、排気効率を上げるためかハニカムをぶち壊して筒抜けにしてありました。
どうやらこの車体のスポーツマフラーが販売されていないか、べらぼうに高額なものしか無いようです。
隔壁によるマフラーの構造はノウハウがないためオーソドックスにパイプの延長で対策しようと考えましたが、ノーマルのマフラーしか取り付けようのないリヤフレームとカウルの形状のため、このような取り回しを余儀なくされました。
これがノーマルのマフラーです。テールカウル下のスペースをいっぱいに使ったデザインです。
マウントはM8ボルト(中央)とM6(前側)2本の3箇所でぶらさがっている形です。
いわゆるマウントブラッケットなるものが無いので、新作マフラーの取り付けに苦労しているところです。
このマフラー単品で重量8.6kg
ライセンスプレートとテールランプをマフラー下に直接取り付ける大胆な構造で合わせて9.6kgになります。
サイレンサーは左右独立したものを連結し、
ジョイントのパイプ2種類と燈火類を取り付ける金具を作りました。
マフラー全体の重量は5.6kgでノーマルより3kgの軽量化になりました。
リヤタイヤエンドから出ないように取り付け位置を決めましたが450マフラー2台分の容積を確保するため、このような大きさになりました。
外側から取り付けボルトにアクセスできない構造なので、取り付け金具の製作に丸二日も費やしてしまいました。
上がってしまったリチウムイオンバッテリーも新品に交換しましたので、明日エンジン始動してみます。
翌日、メインスイッチを入れてセルボタンを押しても、全くセルモーターが回りません。
インジケーターや燈火類は全て正常に動作します。
お客さんにその旨を伝えたら、「持ってくる前からおかしかった」といいます。
「バッテリーあがりかと思っていたがセルモーターが焼きついているかもしれない」とも言われましたので、ここで排気音の確認はできないなと諦めかけていました。
ダメ元でセル始動数回、トライしてみました。
すると1回だけクランクが回転したので、もしかするとOKかもしれないと思い再度トライすると、2回転3回転」と段々回り始めました。5回目くらいにアフターバーンが起きたので確信して、もう1回トライしたら始動できました。
リチウムイオンバッテリーは活性化するのに少し時間が必要らしいです。しばらく電気を流しておくと能力が上がってくる性質です。それとコールドスタートでオイルが固かったことも影響していたと思います。
暖気1分くらいでアクセルあおってみますと、なんとレスポンスのよいエンジンか!ちょい開けで1万瞬時に回ります。音はトルク感ありそうな低音で、思ったほど爆音でないことからサイレンサーの容積が適切であったことが伺えます。ツインエンジンだけどマルチのような吹け上がりです。
延長したリヤバンクのエキパイのはみ出し具合です。カウルの横方向は収まっているのでライディングには影響ないでしょう。
こんなオートバイに比べたら、私の所有車なんてカブみたいなもんです。
スーパーバイクを乗りこなすライダーを尊敬します。私は、このシート片足しか付きません。腕も真っ直ぐ伸ばしてやっとグリップに届きます。
危険なので試乗はやめておきます。
マン島の公道レースについて否定的な意見の人もおられるようですが、正しい論理で批判されているということを理解しながら、現代のモータースポーツと交通社会の係わりについて思うことがあります。
批判の要点は競争社会をベースに市場原理主義の縮図としてライダーや観客の命を軽視した観光産業と言われています。これはマン島TTレースの百年間に224名の死亡者を出しても懲りもせず、毎年危険な公道レースを続け、犠牲になった人は自己責任の名の下に葬り勝者を賛美しているどうしようもない人間の集まりと批評されているわけです。
そのように採られてもしょうがない一面はあると思いますが、これは合法で運営されている以上、日本の道路で交通違反をして事故を起こしている人たちからは批判を受ける筋合いは無いでしょう。私個人的には2輪の運転技術に公道やレース場の境界は無いと思っています。同じ技術をベースに道路に合わせて運転しているだけです。運転技術が高いということはレースの成績が良いことと、公道で安全に運転できるということに相関があるはずです。
日本では毎年1万人位、自動車事故で死亡しているらしいですが、自動車業界こそ競争社会、市場原理主義の象徴と言え、一部の顧客からの危険運転により交通事故が起きている現状をわすれてはなりません。少なくともモータースポーツに参加している人は運転技術の向上を目指して練習しているわけで、練習もしてないで道路で危険な運転をされては危なくて仕方ありません。
クローズドコースにおける技術より公道レースにおける技術の方が実際の交通の流れに入ったときに有効だと思います。実際の生活道路で限界の走行ができるのですから、法廷スピードで走ったときの安全性はレースに参加してないドライバーとは比較にならないでしょう。唯、レーサーだって人間ですから僅かなミスや疲労が重なって、レース中に事故が起きてしまったので、これを批判するよりレース経験も無いのにスピードを出す一般ドライバーに対して指導したほうが効果的というものです。
道路を走行中によく見かけますが、安全な車間距離をとって走行しているのに、周りのクルマよりスピードを出して割り込んでくる輩がいます。衝突しないのは周囲の運転者が避けてくれているだけということを理解する必要があるでしょう。上手い人は他人に不安を与える運転はしないはずです。
本題から離れてしまいましたが、公道バージョンのCRF250Xにレーサー用のサイレンサーを取り付けてみました。
これはお客さんの依頼でエンデューロレースに出るために作ったサイレンサーで、250Xのノーマルより軽いこととパワーも上がっているはずです。
250Xのサイレンサーは米国EPA(環境保護庁)の認定を取っていますが、排気ガスの浄化より、枯れ草に火炎が飛ばないためのスパークアレスターを装備していますのでレーサー用より重いのは仕方ありません。
国内のエンデューロのスパークアレスターは義務付けられていませんので問題ないでしょう。
ワンオフ製作のチャンバーを希望されるお客さんは次のことに、ご注意ください。
製作したいチャンバーの寸法図、または見本が無い場合はお引き受けできません。チャンバーの諸元はエンジンの仕様と密接な関係がありますので、車種毎に専用設計になっています。寸法図が提示されない場合は新規に設計しなければなりませんが、経験の無い車種のチャンバーをゼロから製作するとなると相当な試作とテストを繰り返さなければ、満足な物は作れないでしょう。そういう決まっていない試作などの期間や費用はお約束できるものではないということが理由です。
今回のDT125は全く経験ありませんでしたが、製作できる可能性があったことと、こういう依頼に対応できないと、弊社の存在意義も無いと考えましたので、お引き受けすることにしました。
ワンオフなど安易に引き受けるものではないことを思い知らされる例でした。
DT125といえば水冷エンジンのチャンバーしか経験が無かったのですが、このマシンは空冷エンジンでした。初期型は78年ですがこれは後期型の80年モデルのようです。
依頼内容はRZ125チャンバーのスペックで作りたいということだったのですが、ボア、ストロークが56×50で同じなので使えると思ったのですが駄目でした。ノーマルチャンバーの寸法とRZ用が違い過ぎて、おそらくパワーダウンするだろうと予測したからです。
では空冷エンジンのレーサー用ということで77CR125が56×50で同じボア、ストロークなので使えるのではないかと試作に取りかかったのでした。
これが77CR125スペックですが、試乗してみて落胆しました。
全体的にトルク不足で高速も伸びない、ノーマルより全然走らない失敗作でした。
カタログ値だけの性能比較ですがDTは13PS/7500rpmに対して77CRは22PS/10000rpmということで、同じボア、ストロークでも性能が格段に違うということ。ポート形状やピストン形状など他の要素が大きく違っているためにチャンバー形状も違ってくるということを物語っています。
当時のDTと同じ鋳造型で製造されている80年式YZ125も同じボア、ストロークですが、26.5PS/11000rpmという高回転高出力型の特性を持ちます。一般市販車のDTの性能が違うのは公道での乗りやすさや安全性を重視した結果と考えられますので、やはりノーマルチャンバーをベースに作らなければならないということです。
ノーマルチャンバーは膨張部が2重構造になっていますので、外形寸法からは内部の寸法が測れません。
ストレート部とコンバージェント(収束)コーンは125クラスの過去データーから妥当な寸法を導き出し、推測して決めました。
ようやくワンオフ製作に掛かることができます。
テールパイプがモノクロスサスのショックとクリーナーボックスの狭い隙間をクネクネと曲がって通してあります。こういう部分は実車がないと製作不可能です。
サイレンサーも頼まれましたのでレトロな雰囲気のオールアルミで仕上げました。
試乗してみましたら、ノーマル同様の特性で5000rpmから8000rpmまでパワーバンドが広がる乗りやすいものにできました。
8000rpmからレッドゾーンなので、レーサーのように高回転で回す必要がないエンジンです。
32年前のオートバイなので部品も廃番になっています。壊さないように走り続けていただきたいと思います。
国内のモトクロッサーの排気量では250クラスがスタンダードだと思っていますが、中でも業界のリーダー的存在のホンダが製造しているCRFに力を注いでマフラーを作っています。
2012モデル用ですが
弊社オリジナルの特徴に触れてみたいと思います。
少量生産なのでアルミとチタン板、チタンパイプをハンドワークで加工しています。
フロントキャップの部分です。通常、板物のキャップで作られるパーツですが、アルミ塊から削り出しています。板物の場合、クラッシュして大きな荷重が掛かったときに歪み易いのでアルミ塊の方が荷重に耐えられます。
チタンパイプが圧入してありますが、アルミが熱膨張してパイプが動いてしまうのを防ぐために、キャップ内側にフランジを溶接してボルト止めしてありますので絶対に動きません。
エンドキャップ部分はチタン製です。リヤパイプの内径と長さの適正化により、騒音低減とパワーアップの両立を実現しました。騒音は2mMAX法で楽々クリアします。
菱形断面のアルミパイプは曲率の小さいR曲げと平面の面積を縮小することで、剛性を上げています。ノーマルのアルミサイレンサーより強度が高いと思います。
結合はM5のネジ止めにしてあります。ステレスリベット加締められるエアリベッターがなくてもヘキサゴンレンチだけで脱着できるのでグラスウール交換も容易にできます。
フロントキャップの結合はM6のボルト止めで、こちらもヘキサゴンレンチで脱着可能です。
分解可能にすることで、ダメージを受けたパーツ別に修理したり交換することを前提としていますので、このマフラーのオーナーには、クラッシュしてダメージを受けても使い続けていただきたい思いを込めています。
エキパイとミドルパイプの結合部分はガスケット不要です。
ノーマルのガスケット仕様ですとサブフレームの動きにあわせてサイレンサーも振られますので、ガスケットの内側でエキパイ端末が動いて、潰れてしまっているのを見た事がある人も多いと思います。
0.1mm隙間で嵌め合いしてありますので勘合部分の剛性が上がってパイプ端末が潰れないで済みます。
手曲げエキパイはノーマルと同寸ですが重量は200g軽量、サイレンサーは、なんと1kg軽量になります。
またチタンは錆びないのは勿論ですが、泥汚れもつきにくく、マフラーの素材として理想的です。
製作費はエキパイが2万円、サイレンサーが48000円という量産品並みで提供させていただきますが、ハンドメイドなので納期は業務の状況で変動しますのでメール等でお問い合わせください。
05年の全日本MX会場の和寒でヤマハのパドック前に展示されたアルミ合金製ハイブリッドフレーム。ハイブリッドとはダイキャストや鍛造という異質な製法で作られたパーツの複合体であるという意味。
そして06年モデルとして発売されたアルミフレームのYZ125が最終仕様という認識でした。
これはお客さんがエンデューロ用に購入したマシンです。
実はYZ125チャンバーは高張力鋼管フレームの時代にラインナップしていましたので、エンジンの基本は大差ないだろうという考えで当時もののスペックで製作しました。
最終型のパイプ形状が若干変更になっており、治具に取り付かないので車体合わせのワンオフ製作です。
我社のチャンバーとヤマハエンジンとの相性は良かったと思います。YZ125に乗った忘れられないライダーがいます。
彼を初めて見たのは守谷のコースでした。
KXに乗っていたA級の若手で、千葉の八街市在住ということで名門習志野レーシングかと思っていました。すると翌年YZに乗り換えて、チーム登録は土浦レーシングになっていたライダーの名は斉藤慎也です。全日本A級でチャンバーサポートして最も好成績を挙げてくれたライダーと評価しています。
01年にA級125クラスで4位入賞でしたが、常にトップを狙う意気込みでした。翌年250クラスにステップアップして、YZ250のチャンバーも作りましたが、トップカテゴリーで15位以内ポイント獲得していましたので若手最有力ライダーでした。
当時チームYZでは、ノーマルで勝てるマシンを証明するということで、社外のパーツ装着を一切禁じていましたが、斉藤選手は「チャンバーだけはこれを使わせて下さい」ということをYZのスタッフに願い出て認めていただいたという経緯がありました。
なんと律儀なことか、作ってもらった物に対する思いというか、なんとしても結果を残したいという意欲が他のライダーと違っていたように思います。残念ながら菅生でヤマハの合同練習中に不慮の事故に遭い選手活動に支障を来たして辞める結果になってしまいました。
そのころから、菅生の赤土の路面は予期できない滑りで頭から落下して死亡したり重症にいたる事故が続いたので路面の改善に力を入れ始めたということで、斉藤選手をはじめ、幾人かのライダーが身をもって危険箇所を教えてくれて、路面の改善を実現してくれたものと感じています。
NSR50のロードレーサーが今回の議題。
GPmonoでレースをされているナオキさんの練習車ですが、ミニバイクは転倒も多いそうでダウンチャンバーだと、サイレンサーは路面に擦ってしまうため
サイレンサーをリヤカウルの中を通す、センター出しに改造するためチャンバーをアップタイプに変更してフレームの中を通すレイアウトに作り変えるというもの。
チャンバーを作るとき、最初にやることは元になるチャンバーの寸法を測ってストレート図に書き直すことです。
写真の上側は元のチャンバー
下側はストレート図に基づいて作られた模型
円盤はパイプの内径を表し、軸芯の棒はパイプの長さを表します。
この模型を曲げて車体に取り回すレイアウトを検討します。
このようにエンジンやフレームとの隙間を確認しながら形状を決めていきます。
同じものは二度と作りません。この車両だけのためのワンオフ製作です。
このあとアンダーカウルやキャブレターの燃料ホースなどに当たらないようにクネクネと複雑なカーブを描いて、狭いフレームの隙間にチャンバーが収まっていきます。
明日は模型の形状に合わせてパイプを成型していきます。
成型されたパイプを接合しました。
模型のカーブに似ていますが、車体がアップチャンバーを想定して設計されていないために取り回しはミリ単位でフレームをかわすシビアなものになりました。
アンダーカウル装着のため、フレームギリギリに寄せないと、グラスファイバーのカウルを溶かしてしまうことになります。
明日はラジエターのマウントとセンター出しサイレンサーのフィッティングを行います。
震災の前日から製作に取り掛かっていたタンク作りですが、3日ほど動揺して通常の業務ができませんでした。とりあえず、やりかけた仕事を完了させるべく再開しましたが、計画停電で一日のうち3時間くらいは業務中断になってしまい、非常に効率悪いです。
被災地の電力不足、燃料供給不足を考え、工場の空調や石油ストーブを止めてやっております。幸い寒冷地ではないので、寒いですが我慢しながら仕事しています。これも支援の一つと考えております。
義援金や救援物資だけが災害支援ではありません。最も強力な支援は国の力だと思うのです。自衛隊や消防庁に指令を出したり、車両を動かしたり、職員の人件費を払ったり、全て税金でまかなうのですから被災していない地域の人ができる最も重要なことは、今やっている事業をしっかりと遂行して税金を払うということであると思っています。
アルミ板金でこしらえたガソリンタンク。
オーナーさんはジムカーナでNSR250に乗っていますが、ノーマルタンクの張り出しが大きいことと、エアクリーナー吸気口を塞いだデザインを改善するという目的でタンク製作に踏み切りました。
フィラーキャップはノーマルを使用していますので鍵を使って開閉します。
タンク底板の形状です。エアクリーナーボックスを逃がすデザインです。
中央付近に二つ穴が設けていますが、フィラーキャップの構造上、エアベントと水抜きのパイプがタンク内部を貫通しています。
車体に装着した様子です。
フューエルコックは左下に設置してあります。
レーサー用の部品で、リザーブ無しです。
タンク容量は13L、大体これでご要望にお答えできると思います。
停電や燃料の調達が悪く通常より効率悪いですが、まだまだバックオーダー抱えておりますので、なるべく早く仕事を進めていくだけです。
絶販車のKDX125ですが、時々チャンバー、サイレンサーの製作依頼があります。
車体がなくてはレイアウトが不明のためお断りしてきましたが、今回サイレンサーのみ治具製作してラインナップとしました。
チャンバーはカーブが複雑なので、相変わらず車体持込に限り対応させていただきます。
チャンバーはノーマルのスペックではなくKX125の諸元を用いて、形状をローボーイタイプにモディファイしてあります。
サイレンサー本体はアルミ製、ステンレスパンチングを差し込んで組み立てます。
重量はノーマルが2.2kgに対して0.8kgという軽量さです。
エンドキャップはリベット止めなのでグラスウール交換できます。
価格は¥12000、受注生産で納期は要確認です。
取り付け状態はこんな感じで、
現在バックオーダーで2ヶ月以上かかりますが、お時間に余裕のある方はメール等でお問い合わせください。
時々、質問を受けますので、2ストシングルエンジンのチャンバーをワンオフ製作する場合の費用について通常の解答内容を明記しておきます。
車体持込が前提になりますので、北海道や九州のお客さんから問い合わせられましても対応できかねますので、ご了承ください。
製作の前にチャンバーのスペックを提示いただくか、こちらで過去データーから適当なものをチョイスすることになります。試作テストは別途になりますので既存のスペックによる製作のみ対応します。
新規に製作の場合、型(展開図)を作らなければなりません。型代が¥10000、1本製作でも複数でも変わりません。仮に10本製作なら型代1本当たり¥1000ということになります。
チャンバー本体と型(展開図)
チャンバースペック(寸法)はストレート図で表されているもので、それを車体に合わせて取り回して形状を決定します。
決定したパイプを開いて、展開図となるわけです。
これを罫書きの型として使用することによって同寸のパイプが製作できます。
チャンバー本体の製作費は型が出来ていればシングル1本で¥25000です。
排気量が違っていても工数はあまりかわりませんが、複雑なカーブが多いと¥10000程度割り増しにしていただくこともあります。
ラインナップ品は複数販売できますので、若干割安の機種もあります。
取り付けるサイレンサーが無い場合はサイレンサーの製作も必要です。
最もシンプルなタイプで¥10000です。
チャンバーとの結合はフランジをボルト締めで排気をシールするタイプです。
エンドキャップはリベット止めなので分解してグラスウールを取り換え可能です。
完成すると型代¥10000と品代¥35000でワンオフ製作できます。
材質はSPCC(鉄板)とサイレンサーはアルミを使用した金額です。ステンレスで同スペックで製作の場合は2倍程度かかります。
車体の預かり期間は1週間程度です。
20年経過した車種なので、新規にサイレンサーのラインナップに追加することを渋っておりました。
モトショップ鷹様の熱烈なオファーによりラインナップすることになりました。
上がノーマル、下が今回ラインナップに加えたアルミサイレンサー。
重量はノーマルの2kgに対して、僅か630gという軽量で、重心から遠い車体後部の軽量化に貢献するでしょう。
ノーマルは非分解で生ガスが溜まったら抜けるようにブリザーパイプがついていますが
アルミサイレンサーはリベットをはずして、湿ったグラスウールを交換できるようになっています。価格は特価¥12000也
ですが、現在バックオーダーで2ヶ月分業務が溜まっておりますので3月以降でないと作れませんのでご了承ください。
ラインナップするためには、ノーマルのサイレンサーが取り付くように治具製作しなければなりません。
この治具で位置決めしながら製作しますが
最初は車体に合わせて確認しておかないと
取り付け保証はできませんので、マフラー現品送付でワンオフ製作を希望される場合もありますが、治具製作も含めて了承していただく必要があります。
鷹さんの車両ですが、取り付け確認できると安心できます。
チャンバーとセットでこの様な感じで出来ました。
2スト、旧車のマフラーも続々出てくるでしょう。
現行車は高性能ですが非常に高価格で不景気な今の経済状況だと一部の富裕層しか購入できません。それほどお金かけなくても、いじって楽しめる旧車が時代のニーズに合っているのでしょう。
連日猛暑日であろうと、世間はお盆休みであろうと、私には関係ない。
大勢のお客さんが私の作るマフラーを待っていることも充分承知しているが
どうしてもやらねばならないことがある。
これをつけて走るとどの様な喜びがあるのかは私は知らない。
これは私が考えて作ったものではないが、作った人に再び頼めない理由は
製作者がやめてしまったためであり、既に廃盤の商品になっているからだ。
それなのに、この見本だけで製作に必要な加工寸法を割り出し、材料を選定し、切削工具も購入し
取り掛かっている。
おそらく全工程に費やす時間は100時間を越えるだろう。
時間工賃を1000円で計算しても10万円になるが材料代や工具代は別に実費で払わなければならない。
おそらくこれを希望するお客さんは、そのような計算は一切、頭の中にはないだろう。
もちろん、掛かった全額をお客さんに請求するつもりは毛頭ない。
最初から利益にならない仕事だということを私は分っていたからだ。
それでは何故、儲からない仕事を引き受けたかというと
やってもいないことを、大変だということが嫌いだからだ。
自分がやって経験したことだけが、語っていいことだと思っているからだ。
アルミの塊からマニュアルのフライス盤で削り出す。この加工時間を加工しないで算出できる人がどれだけいるだろうか。これはピボット部分のパーツ
土曜日夕方までかかってここまで出来た。
クッションブラケットとリヤアクスルのパーツ。図面が無いので寸法計測しながら加工していくので
非常に時間がかかる。明日のレースの整備があるので、これにて中断。
本日はアーム製作。
手前がアームの型で、上の4つが絞って出来たアームの部材。
作り方は教えてもよいが、割愛しておく。
よく、作り方を自分で考えないで他人に聞く人がいるが、
調べたり、トライする努力なしに安易に情報を得ようとする行為なので適当に答える。
自分で考えて物事を運ばない人は、新しい物を考案する能力は得られないと考えられるのだ。
アームを溶接で接合してから、スイングアームの形状に合わせて曲げてある。
組み立て治具に各パーツを固定し、仮留めする。いよいよ本溶接ができる状態だ。
溶接完了し、バフ研磨して組み付け確認。
100時間を超える全工程が終了した。オリジナルに引けをとらない仕上がりではないか。
こうして絶版のスイングアームは復刻された。溜まっているバックオーダーが恐ろしい。
依頼されてくる車種は大半がオンロードモデルで今回もその一つ。
フランスヤマハ製で新車で2ストローク車を生産していますが
法律で出力規制が掛かっているとやらで
もう少しパワーアップを希望しているのがお客さんの願いです。
ノーマルのチャンバーからは正確なチャンバー諸元が分りません。
そこで過去の同一排気量のデータから適当なものを選んで
形状を車体に合わせて新作しています。
微妙な変更はテストを重ねないと無理ですが、ノーマルより強力な物にするには
レーサーの諸元を引用することで可能となります。
サイレンサーについても、デチューンの対象ですから排気の抵抗を下げつつ消音効果のある物に作り変えます。
オールアルミでバフ仕上げは2ストモトクロッサーで性能実証済みのアイテムであります。
完成後、チョット公道で試乗してみましたが、美味しい2ストのパワーとサウンドで早くオーナーさんに乗っていただきたいと思いました。
今回の依頼にはオプションがありまして、coocaseというボックスつきリヤキャリアの取り付けです。
ボックスはワンタッチで脱着できてツーリングに買い物に役立ちそうです。
但し、この車両にはボックスを装着できるキャリアが装備されていないので新作する必要があったのです。
グラブレールのねじ穴を利用してボルトオンにしてあります。完璧な立て付けです。(自画自賛)
2010モデルYZ250F用のエキパイをラインナップに加えました。
チタニウム製のエキパイとサイレンサーを50mmショートにしてオリジナルリヤパイプに換装しました
エキパイはノーマルと等長ですがレゾネーター付、実用回転域のコントロール性向上と音量の低減が目的です。
サイレンサーはノーマルで音量に余裕があるのでショート化して排気抵抗を減らす目的です。
チタニウム製のオリジナルリヤパイプは騒音と排圧の調整をしたもので
音量は5000rpmで92dB/AでありますのでMFJのレースでも使用可能です。
気になる価格は、
エキパイ ¥21000(税込み)
リヤパイプ (ノーマルサイレンサー組み換え工賃込み)¥15750(税込み)
大分のホンダウイングイワオ様から特注の製作依頼です。
10モデルCRF250Rのエキパイ製作ですが
ノーマルがステンレスと鉄のフランジに対してチタニウムとアルミフランジでリプレイスします。
チタンパイプφ35とφ38.1の2種類を使います・
片方に蓋を溶接して砂を詰めます。
この砂詰めが不十分だとパイプが潰れたり、皺が入って不良品になってしまいます。
1台分のパイプ代が1万円くらいしますの無駄にすることはできません。
量産のエキパイは100%機械曲げです。
パイプを潰さないように曲げるためにはR曲げ専用の機械が必要で非常に高額な投資になります。
我社は高額な投資はしません。なぜなら、お客さんの必要数は1本だけだからです。
1本だけ曲げるのでしたら、このように万力と炙りバーナーだけで充分です。
180°曲げですが熟練した手曲げ技術がないと高価な材料を何本も無駄にしてしまうでしょう。
これができないとマフラー屋とは呼べませんね。
取り回しは車両がありませんので、このような治具を作って合わせます。
イワオさんからノーマルのエキパイと取り付け状態の画像を送っていただき、それを元に車体との位置関係がうまくいくようにゲージを作っておきました。
曲げたパイプをつなぎ合わせてノーマル形状のエキパイが出来ました。
フランジはアルミ板をフライス加工で作ったものです。
ホンダのモトクロッサーはHRCのキットパーツが別売りされていますので純正部品はコストダウンの対象なのでしょう。
やっぱり他メーカー並みにチタニウムにしていただかないと私の仕事が増えてしまいます。
85ccモトクロッサー国産4メーカーとKTMに対応したチャンバーとサイレンサーを製作し、供給して参りましたが、現在のラインナップは以下のとおりです。
ホンダCR85 チャンバー サイレンサー 04以前、05~モデル
ヤマハYZ85 チャンバー サイレンサー 02~モデル
カワサキKX85 チャンバー サイレンサー 05~モデル
KTM85SX チャンバー サイレンサー 06~モデル
主なレース戦歴
CR85 04,05キッズスーパークロスチャンピオン
CR85、YZ85、KTM85SX 全日本レディースで優勝あり
価格4メーカー共通
チャンバー ¥18000
サイレンサー(MFJ対応) ¥12000税込み 送料別途
全機種受注生産です。納期はお問い合わせください。
そのお客さんは始め電話で場所を確認してからスポーツカー(ロータス)に乗って現れました。
怪しげな工場の下見をしてから注文しようと考えたそうです。
以前、別の業者に品物を注文したがトラブルになってしまい信用できなくなったらしく、製作を依頼するとき慎重にならざるを得なくなったそうです。
それなら大丈夫、信念の仕事をやり通す弊社を選んだあなたは大正解。
必ずや満足させてあげられるでしょう。
最初、装着されていたチャンバーも社外品だったのですが年式も古く錆びている上に素人のような溶接が割れてしまって何度も下手な補修を重ねた痕が見られました。
もちろん修理ではなく新品製作で排気漏れも解消、パワーモリモリのチャンバーがついたRD400がロータスのおじさんの通勤車として走り続けているそうです。
ホンダCRM250は88年に1型として発売開始されました。
94年には3型としてフルモデルチェンジを経て97年からARとして最終型となりました。同車種のチャンバー、サイレンサーのラインナップは3型(RR)とARの2タイプになります。
取り付け寸法が若干違いますので年式を指定していただければ製作可能です。1型と2型はワンオフ扱いになりますので、車体お持込みに限り対応させていただきます。
チャンバーのスペックは2000年CR250Rの寸法でCRMの車体に合わせて取り回ししました。
従いましてノーマルよりレーサーよりのエンジン特性となります。
表面処理はチャンバーがスチールの未塗装とクロームめっきのどちらか選択になります。
サイレンサーはオールアルミ、バフ仕上げが標準です。
価格
チャンバー(スチール)¥24000
クロームめっきは+¥15000
2スト車の車体に4ストエンジンのスワッピング(換装)は何度もやってきた。 しかし今回のスワッピングは今までのとはわけが違う。
これまでのエンジンは旧式の空冷2バルブであったのに対し、これは新型の水冷4バルブだ。 おそらく日本で初めての組み合わせだろう。前後サスペンションはホワイトパワー。リヤはリンクレス。 ブレーキはフォーミュラの対向ピストン。国産には採用されないヨーロッパ製品が目を引く。 画像はエンジンのレイアウトを検討している様子でエンジン位置は決定したがフレームのパイプは繋がっていない。高くなったキャブレターにあわせたエアクリーナーの変更、シリンダーヘッドをかわしたガソリンタンク製作、フレーム中通しの専用エキゾーストパイプetc.難題山積みである。 おそらく実走できるのは夏頃だろう。
この製作計画を聞いて殆どの人は無意味だとか、改造しないでそのまま乗るのが一番いいとか思われるだろう。 実は製作を担当している自分自身も同様に思っていたのだが、製作を諦めさせる説得をしながら、自分の気持ちが完成させて走らせてみたい方向に変化していった。
これを無意味なことと思う人は、マシン選びにどれ程の理由があるだろう。 メーカーのイメージであったりレースで上位を走る機種であったり、バイク店との付き合いであったり。いずれにしても明確な根拠は存在しないはずである。しかも、高額な支払いをして手に入れたマシーンも翌年にはあっさりモデルチェンジされて旧式になってしまう。本当に乗りたいものを決める手段が完全にメーカー任せになっていて、お客さんは踊らされている状態だ。そんな宛がわれたような選択肢では、ただ流行にながされて、他人の真似しかしない日本人の一員になってしまう。
他人と違う方式を試みる精神がこの車両の製作に現れているではないか。 これが完成して走っている姿をみて、どんな乗り味なのか興味を持つ人は多いだろう。しかしその答えは作った者、乗った者にしかわからない領域だ。
無意味だと思う人には一生わからない答えだろう。 そしてこの製作を実現する手段に弊社を選んだ依頼者に満足していただくために腕を振るわなければならない。
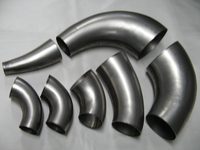
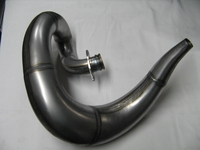
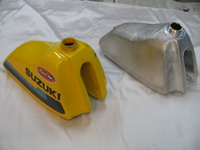

「実用価値の上に、芸術的価値をあわせ備えたとき、初めて完全な商品となる。技術者は科学者の知恵と芸術家の感覚とをあわせ持たなければならない。 」
ここで紹介する製作物 (PRODUCT) はそんな理念の元に追求されたものばかりです。 これら製品の殆どは依頼主のためだけに作られたものですからラインナップしたものは僅かです。
自ら所有したマシンか身近なマシン提供があった場合のみマフラー試作して実走テストを経てラインナップしています。
急な製作依頼、難易度の高い修理等、時間を要することがありますので問い合わせ願います。