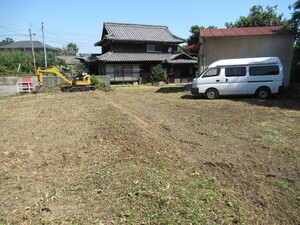
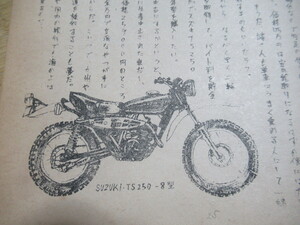
震災の前日から製作に取り掛かっていたタンク作りですが、3日ほど動揺して通常の業務ができませんでした。とりあえず、やりかけた仕事を完了させるべく再開しましたが、計画停電で一日のうち3時間くらいは業務中断になってしまい、非常に効率悪いです。
被災地の電力不足、燃料供給不足を考え、工場の空調や石油ストーブを止めてやっております。幸い寒冷地ではないので、寒いですが我慢しながら仕事しています。これも支援の一つと考えております。
義援金や救援物資だけが災害支援ではありません。最も強力な支援は国の力だと思うのです。自衛隊や消防庁に指令を出したり、車両を動かしたり、職員の人件費を払ったり、全て税金でまかなうのですから被災していない地域の人ができる最も重要なことは、今やっている事業をしっかりと遂行して税金を払うということであると思っています。
アルミ板金でこしらえたガソリンタンク。
オーナーさんはジムカーナでNSR250に乗っていますが、ノーマルタンクの張り出しが大きいことと、エアクリーナー吸気口を塞いだデザインを改善するという目的でタンク製作に踏み切りました。
フィラーキャップはノーマルを使用していますので鍵を使って開閉します。
タンク底板の形状です。エアクリーナーボックスを逃がすデザインです。
中央付近に二つ穴が設けていますが、フィラーキャップの構造上、エアベントと水抜きのパイプがタンク内部を貫通しています。
車体に装着した様子です。
フューエルコックは左下に設置してあります。
レーサー用の部品で、リザーブ無しです。
タンク容量は13L、大体これでご要望にお答えできると思います。
停電や燃料の調達が悪く通常より効率悪いですが、まだまだバックオーダー抱えておりますので、なるべく早く仕事を進めていくだけです。
91年頃、会社員として最後の仕事。当時ホンダがエンジン供給して英国ローバー社で自動車を生産していましたが、次のプロジェクトは英国で完成車工場を立ち上げることでした。エンジン工場はすでに稼動していましたが、車体工場は全くの更地の状態。部品メーカーの選定や打ち合わせ、職場に導入する設備の調達などの目的で英国に長期滞在していたころの話です。
勤務先のホンダオブUKは土日休日のため
休日は社用車を借りて観光です。
これはバッキンガム宮殿前、エリザベス女王の住居ですね。
イギリスは道路が発達していてロンドンを中心としたリングロードと放射状に伸びたモーターウェイは日本が明治時代に首都圏の道路の構造を参考にしたというほど昔から完成されたものでした。
移動の殆どは社用車で行うのですが、ロードマップを見ながら好きなところへ行きます。
大抵の日本人はゴルフ三昧で、サマータイムの時期は、夜10時ころ日没なので平日でも夕方からコースへ出てラウンドできるくらい昼間が長いのです。冬は逆ですけど
朝は3時から明るいですし、一日が非常に長く感じられます。
英国は街ごとにレース場がある感じです。
国土が適当なアップダウンがあって樹木が少ないのでMXコースが自然の地形のままできるのです。一日に何回も小雨と晴れが繰り返す天気なので、コースコンディションが常に良好なのです。
それからオートバイメーカーの多さでは日本の比ではありません。さすが産業革命の国、日本メーカーは英国車の真似をすることからオートバイ製造が始まったのでしょう。
そして、ライダーの体格。250ccのマシンがまるでミニバイクのように見えます。この男たちとぶつかり合うことが日本人にとってどれだけ不利なことか、この男たちの体格を見れば想像がつくでしょう。
ブリティッシュチャンピオンシップのスタートです。美しい緑のコース、どこでもこんな感じでパドックも観客席も緑の草で覆われています。
人口的なセクションを作らずとも、ダイナミックなコースができています。
英国ではライダーのことをジョッキー(騎手)と呼びます。オートバイが馬の代わりであることを示す文化の象徴でしょう。
このレースのスピードを観て、当時全日本チャンピオンだった宮内選手が彼らと走ったとして、はたして通用するだろうか?と思いを馳せましたが、その答えは翌年、鈴鹿サーキットで開催された世界選手権で答えを知ることができました。
プライベーターのマシンと思われますがメーカーのロゴを大きくアピールしたグラフィックはヨーロッパからの発案でした。
日本ではこのようなオリジナルのデカールなどはワークスマシンだけのことで
市販車に貼るデカールなどは全く見られませんでしたが、英国では既にオリジナルデカールが多数販売されていました。
レース場の売店で現地のオリジナルデカールを購入して自分のマシンに貼っていました。
日本ではこれが最初だったでしょう。
テクノセルというノンスリップ加工のシートレザーも現地で仕入れてきました。
マシンは91年型CR125Rですが、長期出張で練習不足。この年は殆どレースにでられませんでした。
それが会社を辞めることになった一因かもしれません。
レースの開催日や場所は現地のオートバイ雑誌を購入して調べて行っていましたが、その雑誌の記事のレベルが日本のものとは隔絶したものを感じました。例えば素人向けのメンテナンス講座などではなく、本職のオートバイ屋が参考にできるような解説とか。
ステアリングヘッドのベアリングの圧入が緩んでしまった場合のバックアップの方法とか、燃焼室のスキッシュの変更とその効果や排気ポートにサブチャンバーを追加して容積を変更する手法とか、実戦で培われたメンテナンスやチューンアップの方法が惜しげもなく紹介されていて、大変面白かったことを覚えています。さすがモータースポーツ先進国です。
これは世界選手権125ccクラスのステファン・エバーツの走りです。
当時16歳でしたが、こんな速い125ccの走りは他に見たことがありません。
確かこの年、初チャンピオンを獲得しています。
他にも日本では見られない500ccのGPも観ましたがCR500の市販車でチャンピオンだった、ベルギー人ジョージ・ジョベも観ることができました。
これはF1、イギリスGPでシルバーストンに行ったときのスナップ。
コースサイドまで自由に入って芝生でくつろぎながら観れます。現地の応援団は凄まじく、自国のドライバーに対する声援はF1サウンドに引けをとりません。
観戦のしやすさは鈴鹿とは比較にならないでしょう。コースの近くに駐車場も沢山あるので、当日渋滞もなくゆっくり来れますし、チケットも当日、自販機で購入して即入れます。
このレースはウイリアムズのナイジェル・マンセルの母国GP優勝でした。
帰国してしばらくして、当日の朝まで極秘でVIPが狭山工場に訪問すると聞いていました。セキュリティーのためか当日、知らされたVIPの名前はチャールズ英国皇太子妃ダイアナさんでした。
間接部門から歓迎のため100人ほど選抜されて出迎えしました。
ダイアナ妃もモータースポーツ好きでクルマの生産現場を見たいということで、東京から一番近い本田の狭山工場に白羽の矢がたったのでしょう。F1のエンジンを英国のコンストラクターに供給していることも関心を持たれた要因でしょう。
無線で「ただ今関越道川越インターを通過」という連絡が聞こえ、間もなく前後を警視庁のパトカーに護衛されたロールスロイスに乗ってダイアナ妃が入場されました。パトカーはニッサンスカイラインだったことが残念ですが、警視庁もレジェンドのパトカーを用意してもらいたかったですね。クルマから降りてきたダイアナ妃はどの男性従業員より背が高く見えましたが、もともと180cmでハイヒールをお履きですから、かないませんね。
MXの修行にアメリカを選ぶ人が多いですが、アメリカは広すぎて田舎です。イギリスはモータースポーツが凝縮されていて技術的に濃い感じがします。世界でリーダーシップを取るには、世界を知らなければならないでしょう。
オール読物新人賞作品、佐々木譲原作の小説を、にっかつが実写化したビデオフィルム。
この映画封切り当時、80年ころだったと思いますが、オートバイ誌で上映されていることは知っていましたが観ることはできませんでした。それもそのはず、ポルノ映画の劇場でしか上映されていなかったので学生だった私はどこでやっているかわからなかったのです。
最近になって埼玉ラングラーズ・・・もとい、チェッカーズの島田さんからお借りして観賞できました。
主演:石田純一(新人)が岩田貞二役、洋子役が熊谷美由紀(故松田優作夫人)という大物役者を起用しています。
2輪を題材にした映画で好きなのは「汚れた英雄」と「マッドマックス」でしたが、これを観てからは後世に残したい2輪映画として一番に挙げたいと思いました。
時代背景がモトクロスを始めたころの私たちと全く同じで、しかも練習場として映像にも登場する、吉見のコースや高坂のコースが写っているばかりか、セーフティーパーク埼玉や鈴鹿サーキットのレースシーンもたっぷりと収録されています。
しかも、映画の取材も行われたチェッカーズの原口選手や石神選手がライダー役を務めていたり、岩田貞二のライバルの根元役は鈴木秀明選手という豪華な顔ぶれで、これはフィクションではなく実録といっても過言ではありません。
基本はポルノ映画なので、貞二と洋子は本田航空の滑走路脇でラブシーンとなりますので18禁ですが、今時の中高生はもっとすごいの見てますから問題ないでしょう。
埼玉では新入社員が筆おろしに行く大宮にある劇場に、取材協力したチェッカーズ御一行が上映中の鉄騎兵を観にいったところ、サトケンが入籍前の水沢アキ似の彼女と同じ劇場にいるところを発見したというエピソードを聞きました。
実際に開催されていた東京ダイナミックシリーズというレースシーンの設定で本物のプロライダーのパドックも写されています。
若き日の鈴木秀明選手と唐沢栄三郎選手。
私が初めてライディングを教わったA級ライダーは唐沢さんでした。今でもその教えは忘れていません。
貞二が所属している埼玉ラングラーズですが、推測ですけど
私が会社就職して初めて買ったマシンが83CR250だったのですが、そのお店が東京のモトバムでそこのチームスポンサーがラングラーというジーンズのメーカーだったことと、モトバムの代表池沢さんがモーターレク推進本部の出身でしたから映画製作に関って埼玉ラングラーズと命名したのでしょう。ホンダはスポンサーでないようですのでモトクロス界に顔の効く人が身内だけで好きな映画を作ったということでしょう。
映画のラストシーンはヨコハマ杯鈴鹿サーキット大会で貞二が優勝できなかったらモトクロスを辞めるという設定でしたが、惜しくも最終コーナーでライバル根元にかわされて2位でした。
私は是非、現代判「鉄器兵、跳んだ」を制作してもらいたいと思いました。石田純一と熊谷美由紀が子供を作り、モトクロスでA級ライダーを目指す物語を・・・
昨年末にピストン交換とヘッドメンテナンスしたので、新しいうちにパワーチェックしてみました。
CRF150Rの主要諸元によりますと最高出力24.5ps/12500rpm、最大トルク1.47/10000rpm
ということですがカタログ数値はカウンター出力(エンジン動力計による測定)である場合が多く後輪出力よりも数値が高く表示されているはずです。しかも上記の数値は2006年当時の96dB仕様のマフラーで現行の94dB仕様とは異なるデータに違いありません。実際のパワーは駆動系のパワーロスを含みますので実測の数値を知っておくことがチューニングの指針になることは明らかでしょう。
測定は我社から徒歩2分という近さのmotoGLADさんに依頼しました。マシンを押して行けるほどの距離にあります。
motoGLAD店舗風景
日光街道杉並木(R407)沿い
我社から国道を隔てた向かい側に位置しておりオンロード系の販売、整備
レーサーの製作などが主な仕事です。
ダイノジェット測定室です。
マフラーに差し込まれているのはA/Fセンサーで回転数毎の空燃比も同時に測ります。
CRFはダイレクトイグニションのため回転数のパルスをコイルから検出できません。コイルにつながるハーネスを調べてCDIユニットのカプラー付近から検出できました。
測定は2タイプで行いました。
昨年使ったモディファイ品とSTD品をそれぞれ付け替えてみました。
普段走行に使用している状態と完全ノーマル仕様の出力カーブとA/Fを把握することが今回の目的です。
エンジン温度の変化によっても数値が変動するということで、熱ダレしてくると数値が下がってしまうということもあり、1時間くらいの冷却時間を空けて別々に測定しました。
モニターの画像は左がスピードメーター、
右がタコメーター、下の横長のグラフが
Air、Fuel Ratio(空燃比)を表しています。
運転状態をリアルタイムで確認できます。
測定データーはパソコンに保存されプリントアウトできますので次に説明します。
完全ノーマル仕様のグラフ
MAX POWER=20.3PS
9500rpm付近がピークで緩やかに下がっていきます。レブリミットは13500rpm
MAX TORQUE=1.3kgm/ 12500rpm
上の曲線は馬力のデータ、下の曲線はトルクのデータを表しています。
その下はAFレシオ(空燃比)データを表しています。
20年経過した車種なので、新規にサイレンサーのラインナップに追加することを渋っておりました。
モトショップ鷹様の熱烈なオファーによりラインナップすることになりました。
上がノーマル、下が今回ラインナップに加えたアルミサイレンサー。
重量はノーマルの2kgに対して、僅か630gという軽量で、重心から遠い車体後部の軽量化に貢献するでしょう。
ノーマルは非分解で生ガスが溜まったら抜けるようにブリザーパイプがついていますが
アルミサイレンサーはリベットをはずして、湿ったグラスウールを交換できるようになっています。価格は特価¥12000也
ですが、現在バックオーダーで2ヶ月分業務が溜まっておりますので3月以降でないと作れませんのでご了承ください。
ラインナップするためには、ノーマルのサイレンサーが取り付くように治具製作しなければなりません。
この治具で位置決めしながら製作しますが
最初は車体に合わせて確認しておかないと
取り付け保証はできませんので、マフラー現品送付でワンオフ製作を希望される場合もありますが、治具製作も含めて了承していただく必要があります。
鷹さんの車両ですが、取り付け確認できると安心できます。
チャンバーとセットでこの様な感じで出来ました。
2スト、旧車のマフラーも続々出てくるでしょう。
現行車は高性能ですが非常に高価格で不景気な今の経済状況だと一部の富裕層しか購入できません。それほどお金かけなくても、いじって楽しめる旧車が時代のニーズに合っているのでしょう。
MTBプロライダー、日本人として始めて海外メーカーと契約し世界選手権を走った世界ランカー。
アジア選手権2連覇、JCFシリーズチャンピオンなど輝かしい戦績をもつダウンヒルライダー
井出川直樹選手はホンダレーシングとも契約してRN01で戦ったこともある。
現在、彼は京都のダイアテックと契約し、カナダのEVIL(イービル)というメーカーの自転車に乗っている。
しかし、このEVILは国内に1台しか輸入されておらず、
即ち井出川選手専用のプロトタイプでスペアマシンもない。
これが、EVIL社スイングアーム、部品単価は聞いてないが、メインフレームだけで40万円くらいだそうだ。
これをハンドワークで1品だけ製作頼まれても、この前のスイングアームより3倍くらい手間が掛かりそうだ。大体、切削部品をこのクオリティで仕上げるにはNC(数値制御)マシンに頼るしかないわけだが、NC加工の工賃は段取り1回の金額なので1個加工するのと50個加工するのとあまり変わらないので、1個だけ加工すると莫大な金額になってしまうので普通はやらない仕事だ。
幸いこれは2箇所のヘアクラックを補修するだけなので問題はない。
クラック2箇所、塗装を剥離してからTIG溶接することになる。
亀裂を溶接だけでは再び発生してしまうだろう。
再発防止のために補強パッチを追加しておく、これで寿命は格段に向上するはずだ。
こちらはビード肉盛りで様子をみる。
このスイングアームは左右非対称な接合方法で、こちら側だけ突き合わせになっていることが
強度不足の原因とおもわれる。
高負荷の足回り部品を溶接する場合、荷重の方向に対してなるべく長手方向に接合することが
セオリーなのであるが、突き合わせが最も不利な条件なのである。
いずれにしても日本屈指のダウンヒルレーサーが溶接修理を頼ってきてくださったことに感謝いたしまする。
連日猛暑日であろうと、世間はお盆休みであろうと、私には関係ない。
大勢のお客さんが私の作るマフラーを待っていることも充分承知しているが
どうしてもやらねばならないことがある。
これをつけて走るとどの様な喜びがあるのかは私は知らない。
これは私が考えて作ったものではないが、作った人に再び頼めない理由は
製作者がやめてしまったためであり、既に廃盤の商品になっているからだ。
それなのに、この見本だけで製作に必要な加工寸法を割り出し、材料を選定し、切削工具も購入し
取り掛かっている。
おそらく全工程に費やす時間は100時間を越えるだろう。
時間工賃を1000円で計算しても10万円になるが材料代や工具代は別に実費で払わなければならない。
おそらくこれを希望するお客さんは、そのような計算は一切、頭の中にはないだろう。
もちろん、掛かった全額をお客さんに請求するつもりは毛頭ない。
最初から利益にならない仕事だということを私は分っていたからだ。
それでは何故、儲からない仕事を引き受けたかというと
やってもいないことを、大変だということが嫌いだからだ。
自分がやって経験したことだけが、語っていいことだと思っているからだ。
アルミの塊からマニュアルのフライス盤で削り出す。この加工時間を加工しないで算出できる人がどれだけいるだろうか。これはピボット部分のパーツ
土曜日夕方までかかってここまで出来た。
クッションブラケットとリヤアクスルのパーツ。図面が無いので寸法計測しながら加工していくので
非常に時間がかかる。明日のレースの整備があるので、これにて中断。
本日はアーム製作。
手前がアームの型で、上の4つが絞って出来たアームの部材。
作り方は教えてもよいが、割愛しておく。
よく、作り方を自分で考えないで他人に聞く人がいるが、
調べたり、トライする努力なしに安易に情報を得ようとする行為なので適当に答える。
自分で考えて物事を運ばない人は、新しい物を考案する能力は得られないと考えられるのだ。
アームを溶接で接合してから、スイングアームの形状に合わせて曲げてある。
組み立て治具に各パーツを固定し、仮留めする。いよいよ本溶接ができる状態だ。
溶接完了し、バフ研磨して組み付け確認。
100時間を超える全工程が終了した。オリジナルに引けをとらない仕上がりではないか。
こうして絶版のスイングアームは復刻された。溜まっているバックオーダーが恐ろしい。
スズキRMの前のモデルはTMという名称でした。昭和38年生まれの私でさえ乗ったことがありません。
エンジンや車体はほぼハスラー250ではないかと思います。ハスラー90は持ってましたけど、何処へやってしまったかさえ覚えていない遠い昔のことになってしまいました。
さて今回の製作依頼はTM250のチャンバーです。下に置かれた純正品が老朽化のため新作することになりました。
当時のレーサーはサイレンサーもありませんが、テールパイプにスプリングフックは付いているので
オプションでサイレンサーを装着できたのでしょう。
潰れたノーマルチャンバーを元に採寸して製作したニューチャンバー。
口元フランジも絶版ということで、新作し、ニューチャンバーとセットになります。
採寸した諸元はこのようにガバリを作成して鉄板に罫書いて製作します。
レストア中のこのマシン、クランクケースもOH中なので内部が確認できますが
これはプライマリーキックではないことが分ります。
最近のオートバイは全てプライマリーが当たり前になっていて、ギヤが入っていてもクラッチを切ってエンジン始動ができる構造になっています。
それはキックギヤとクラッチアウターのギヤの間にプライマリーギヤが存在してメインシャフトの連結をクラッチで解除しながらクランクギヤを回せることで、ギヤが入っていても始動できるわけです。
しかしTMにはプライマリーギヤの軸穴が存在しないことが右ケースを見れば分ります。
キックギヤとカウンターシャフトのギヤが直結の構造です。
即ち、ギヤをニュートラルにしてからキック始動できたということです。
ギヤが入っていれば押しがけはできますから、ロードレースでも押しがけスタートが主流でした。
モトクロスでは、今のようなスターティングマシンは無く、エンジンを止めた状態でオフィシャルの日章旗を振る合図でキックスタートでレースしていました。
当然、右足でキックして、左足でギヤを入れてスタートするわけですから、予めギヤをいれてキックできるプライマリー車の方がスタートが優位だったわけです。
古いマシンを乗っている人を見て、「新型のマシンの方がいいよね」という人がいますが
これは古い名作映画を観たり、懐かしい歌謡曲を聴いたりするのと似ていると思うのです。
新型が性能がいいのは当たり前、いつまでも自分の青春時代のマシンを楽しんでいたいという欲求があることを非常に理解できます。
このダウンチャンバーのリバイバルは口元フランジとサイレンサーも新作で3台分同時に、しかも前金で依頼されていますので、他の仕掛かり業務も含めて8月中に急な依頼がありましてもお引き受けできませんのでご了承ください。
泣く子もだまる(そんなわけない)国際B級(掃いて捨てるほどいる)時代の私。
マシンは我社(前の勤め先)で製造したCR250R、88モデル
コースは成田エアポートMXランド。
ジュニア時代、87年全日本MX第1戦桶川大会の予選1組。
マディーの予選を制したのは私。最も勢いのあった頃だった。
スタートを正面から見た様子。既に1コーナーへ向けて最短コースへ加速している。
マディでトラクションさせる能力に秀でていたに違いない。
ジュニア125クラス決勝は残念ながら転倒で16位に終わってしまったが
MXキャリアの中で最も充実していた時期なので忘れることはできない。
狭山レーシングのエース、井本敬介選手。87年は国際A級2年目
この年の前期は全員125ccでのレースだった。
朝霞研究所、第2研究ブロック操安グループに席を置き後にCRFシリーズの開発責任者になられた。
奥にチームグリーンの岡部篤史、長沼朝之、隣に無限の鶴田忍の姿が見える。
市販CRでワークスライダーに引けをとらない堂々とした走りだった。
井本氏の指導がなければ私の国際B昇格も無かったかもしれない。
84年関東選手権、予選10組時代。あの頃はとにかく必死だった。
予選を通過しないことには決勝は走れぬ。
あの頃の経験があったからこそ、今の自分がある。モトクロス最高!
依頼されてくる車種は大半がオンロードモデルで今回もその一つ。
フランスヤマハ製で新車で2ストローク車を生産していますが
法律で出力規制が掛かっているとやらで
もう少しパワーアップを希望しているのがお客さんの願いです。
ノーマルのチャンバーからは正確なチャンバー諸元が分りません。
そこで過去の同一排気量のデータから適当なものを選んで
形状を車体に合わせて新作しています。
微妙な変更はテストを重ねないと無理ですが、ノーマルより強力な物にするには
レーサーの諸元を引用することで可能となります。
サイレンサーについても、デチューンの対象ですから排気の抵抗を下げつつ消音効果のある物に作り変えます。
オールアルミでバフ仕上げは2ストモトクロッサーで性能実証済みのアイテムであります。
完成後、チョット公道で試乗してみましたが、美味しい2ストのパワーとサウンドで早くオーナーさんに乗っていただきたいと思いました。
今回の依頼にはオプションがありまして、coocaseというボックスつきリヤキャリアの取り付けです。
ボックスはワンタッチで脱着できてツーリングに買い物に役立ちそうです。
但し、この車両にはボックスを装着できるキャリアが装備されていないので新作する必要があったのです。
グラブレールのねじ穴を利用してボルトオンにしてあります。完璧な立て付けです。(自画自賛)
2010モデルYZ250F用のエキパイをラインナップに加えました。
チタニウム製のエキパイとサイレンサーを50mmショートにしてオリジナルリヤパイプに換装しました
エキパイはノーマルと等長ですがレゾネーター付、実用回転域のコントロール性向上と音量の低減が目的です。
サイレンサーはノーマルで音量に余裕があるのでショート化して排気抵抗を減らす目的です。
チタニウム製のオリジナルリヤパイプは騒音と排圧の調整をしたもので
音量は5000rpmで92dB/AでありますのでMFJのレースでも使用可能です。
気になる価格は、
エキパイ ¥21000(税込み)
リヤパイプ (ノーマルサイレンサー組み換え工賃込み)¥15750(税込み)
現代の2輪車は大型車から原付自転車まで燃料噴射を標準装備する時代。
4輪車は30年ほど前からキャブレターから燃料噴射へ移行していたのに2輪が遅れていた理由が解ったような気がする。
最大の理由は排出ガス規制に対応することにあった。
2輪の場合は規制が強化されたのが最近であることと、4輪のような高性能な燃料噴射装置を採用する車体のスペースと販売価格の低さが、開発の遅れとなって表れたのだろう。
地球温暖化の対策や低公害、省エネのために自動車会社の出した答えはハイブリッド車に並んで
高性能な燃料噴射装置の開発であった。
コモンレール式燃料噴射とピエゾ素子インジェクターが現代最高の環境対応技術といえるだろう。
ピエゾ素子は圧電素子の一種で、応力を加えると電流が起きる物質の総称で
温度、加速度、超音波など各種センサーに使われたり、身近なところにはエプソン、リコー、ブラザー社のインクジェットプリンターはピエゾ素子を使ってインクを噴射している。
写真のような精巧な噴射制御が出来ることからも、燃料の噴射制御も正確に行えることが想像できる。
原始的な燃料噴射は機械式の燃料ポンプで燃圧を上げて、バネで閉じられた弁を圧力で開けて噴射する方式。当然、正確な噴射はできなかった。
燃料の排ガスに与える影響は濃い過ぎるとPM(黒煙)が出たり、燃焼温度が上がってNOxが増加する。薄すぎると出力が出ない、不完全燃焼でCOやHCが増えるといったところ。
コモンレール式燃料噴射は蓄圧式とも呼ばれ、燃料ポンプが単なる燃料の供給ではなく、最新式では2000気圧という超高圧で燃料を加圧して、インジェクターに供給する。
酸素やアルゴンなど高圧ボンベが150気圧なので、その10倍以上だ。
何故そのような高圧が必要かというと、圧縮された燃焼室に微細な粒子として燃料を噴射させるためである。粒子が微細なほど燃焼という化学反応が迅速かつ確実に行われ、出力の向上と排ガスの清浄化に役立つのだ。
それからピエゾ式インジェクター、これは従来のソレノイド(電磁式)バルブに比べ、応答が速いのが特徴で
最新のソレノイドでも1回の燃焼に1から3回の噴射に対してピエゾ式は最高で7回の噴射が可能だという。
噴射間隔でいうとソレノイド式が900分の1マイクロ秒、ピエゾ式が1万分の1マイクロ秒である。
この1燃焼に対して多段噴射が必要な理由は、燃焼を段階的に発生させることで、完全燃焼と燃焼温度を低減させることだ。
そのために、コモンレール式燃料噴射とピエゾタイプインジェクターが不可欠ということだ。
残念ながら製造コストが非常に高価で、おそらくシステム全体で自動二輪車1台分くらい必要だろう。
それ故、2輪車にこれが採用されることは現実的ではない。
最初にコモンレール式燃料噴射を量産したメーカーは1995年、デンソーである。
主にトラックの直噴用で車両価格が1千万円クラスなので採用できただろう。
それに対して高級乗用車をターゲットにコモンレール式を量産したのがボッシュだ。
BMWやメルセデスベンツなので高額なシステムでも全体の割合からすると大したことはない。
遅れをとって後にトヨタレクサスにもデンソーのシステムが採用された。
我々の興味があるのはオフロードレーサーの燃料噴射システムだが
認定モデルではないため、排ガス規制の対照ではない。
したがって、高額な投資をして燃料噴射を開発する必要がない、キャブレターでも充分な性能が出せるなど、4輪のような高性能な噴射装置は装備しないだろうと考える。
4輪のような燃焼室直噴も聞いたことがないし、吸気通路に空気と混ぜてポートから吸入する
ウォールガイド式(空気流動で成層化)が主流だろう。
これが進化すると、ストイキ直噴(理論混合比で成層化)、スプレーガイド式直噴(高圧で噴霧で成層化)ということになり、吸気管内方式と比較して15%も燃費低減できるという。
こういうわけで、全ての認定車が燃料噴射に移行してきたように、車両価格の高いレーサーから燃料噴射化が進んでいくのが時代の流れなのだろう。
いずれ小排気量車も製造コストの問題が解決次第、移行することになるだろう。
松山オートテックは愛媛県松山市の山中にあるMXコースで、県民の水瓶「石手川ダム」をさらに山奥へ進むと、瀬戸内海が広がる絶景の山の尾根の部分を切り崩したMX場が現れる。
ゴルフ場も隣接しているのでコースまでの道路は完全舗装された環境のよさ。当時のMXファンなら五明(ごみょう)という地名で知られている、そのコースは通称パチ台と呼ばれていて
コースの一番低い位置にスタートとフィニッシュジャンプがあり、高低差100mくらいの斜面を一気に上ってからパチンコ台のようにクネクネとバンクのついたタイトコーナーを曲がりながら下ってくるので
下からコースの状態が80%くらい見えるので観戦しやすいコースだった。
松の木の山林に黄色い山砂のコースは日本のMXコースの中でも一番美しかっただろう。
そしてカワサキ ダートクルニクルスの記事を読んでいて懐かしく思った。
チームグリーンの平井監督の話だったが、最初に育てたA級ライダーは中深迫正と菅原義広。
その前にチームグリーンとして成功したのがスーパーノービス調所伸一と鈴木南平だったことを
平井監督が語っている。
そして、その舞台が全日本四国大会の松山オートテック、83年のレースだった。
コースの一番高いストレートが終わった左コーナーの向こうは青い瀬戸内海が見えるはずだが
ライダーにはそんな景色は目に入らない、バンクのコーナーを立ち上がったら、菅生の大坂より長い下りジャンプが待っているからだ。
そのジャンプを最初に飛び出してきたのが、調所伸一と鈴木南平のカワサキだったわけだ。
私も鮮明に覚えている。現地には行っていないがライディングスポーツ誌の見開き2ページを飾った写真が、その場面だったからだ。
調所選手の逸話は、桶川のレースで優勝したあと、「フロントフォークがいつもと違う」と言ったので
フロントフォークをばらしたら、片方のフォークにオイルが入ってなかったという話。
片方のオイルがなくても勝てるくらい速かったということだ。
鈴木選手はバイクランドジャパンの御子息、木更津サーキット(イーストバレー)や飯倉スポーツランドも経営していた、あの鈴木さんである。
2人は早くMXに見切りをつけて別の道に進んだと聞いたが、ワークスライダー養成チームとしてのチームグリーンの活躍の原点は彼らだったに違いない。
ハンチング帽にサングラス姿の平井監督は全日本MXの名物となっていた。そんな平井監督と私は一言だけ会話したことがある。
86年の国際B級ゼッケン2はクレイジー安藤さんだ。
安藤さんは石神覚さんのポイントワンに所属していたころから狭山レーシングと縁があり、
カワサキに乗り換えてジュニアライダースに所属してからも、狭山のトラックで全日本遠征していた。
菅生の全日本のときB級の予選でサインエリアにいたとき、平井監督が私に「安藤は予選通過したかー」と尋ねられた。「ハイ、通過しました!」 たったこれだけだが忘れられない。
国際Aは私にとって神様だ、そして監督は神様を育てている創造神なのだ。
安藤さんは前年、カワサキに乗り換えて鈴鹿で4位に入った。申請すればA級昇格できたのだが
「申請A級はインチキだ」と言って翌年、優勝するつもりでいたのに成績不振で折れてしまったのだ。
平井監督はカワサキに乗って速かった安藤さんにも期待をかけていたのだろう。
話は逸れてしまったが
松山オートテックは85年、先輩の井本さんがB級ゼッケン9の年に全日本四国大会として最後のレースを開催した。
その日のマーシャルは四国のトップライダー三原達夫。
国際Bの公式練習は三原選手と井本選手の一騎打ちだった。
四国選手権のトップライダーの松山でのスピードを見せ付けたいという思いと
一桁ゼッケンが田舎B級に負けてはいけないというプライドが、走りに表れていた。
そして、三原選手の御子息は後にチームグリーンへ入るほど成長し、親の意思を継いだと思われる。
その選手の名前は三原拓也、四国で8番目の国際A級ライダーとなった。
A級250でヒート優勝したのがMX界1のイケメン立脇三樹夫選手だったのが印象的だった。
その後はゴルフ場建設予定地になってしまい閉鎖したと聞いている。
【サイドビュー】
【サイドカバーはずし】
【リアフォーク・スプロケット】
150R最大の欠点であるリヤフォークの強度不足を対策した補強リヤフォーク。
7Nー01材で曲げ応力が最大になる箇所の断面積を30%増して対応している。
町工場はメーカー任せにする必要はないのだ。
一見スペシャルのスプロケットはノーマルベースで112個の穴空けをして軽量化した。
ノーマルはなんと、820gも重量があるのだが、570gまで落とした。
しかし、タロンのアルミは270gしかないので2倍の重量だ。(残念)
但し、耐久性は3倍くらい期待できるので、コストパフォーマンスで断然勝っているはずだ。
テスト中の新型構造はマフラー内部で二股に分岐させ、2本のパンチングパイプを通って排気され
る。
ノーマルの開口面積と同等の2つ穴にした場合、約1dB排気音が上がることが分かった。
排気を2列にすることで排気ガスの流速があがるためと思われる。
これがパワー的に有利だということを示しているのだが、あとは、パイプ径の調整をすれば音量のコントロールも可能だ。
とにかく、いつも同じマシンに乗っていたのでは、ライディングそのものの情熱が冷めていってしまうので 常に新しい試みと、ベストコンディションを保つメンテナンスを怠らないことがモトクロスを長く楽しむ秘訣ではないかと思う。
2スト車の車体に4ストエンジンのスワッピング(換装)は何度もやってきた。 しかし今回のスワッピングは今までのとはわけが違う。
これまでのエンジンは旧式の空冷2バルブであったのに対し、これは新型の水冷4バルブだ。 おそらく日本で初めての組み合わせだろう。前後サスペンションはホワイトパワー。リヤはリンクレス。 ブレーキはフォーミュラの対向ピストン。国産には採用されないヨーロッパ製品が目を引く。 画像はエンジンのレイアウトを検討している様子でエンジン位置は決定したがフレームのパイプは繋がっていない。高くなったキャブレターにあわせたエアクリーナーの変更、シリンダーヘッドをかわしたガソリンタンク製作、フレーム中通しの専用エキゾーストパイプetc.難題山積みである。 おそらく実走できるのは夏頃だろう。
この製作計画を聞いて殆どの人は無意味だとか、改造しないでそのまま乗るのが一番いいとか思われるだろう。 実は製作を担当している自分自身も同様に思っていたのだが、製作を諦めさせる説得をしながら、自分の気持ちが完成させて走らせてみたい方向に変化していった。
これを無意味なことと思う人は、マシン選びにどれ程の理由があるだろう。 メーカーのイメージであったりレースで上位を走る機種であったり、バイク店との付き合いであったり。いずれにしても明確な根拠は存在しないはずである。しかも、高額な支払いをして手に入れたマシーンも翌年にはあっさりモデルチェンジされて旧式になってしまう。本当に乗りたいものを決める手段が完全にメーカー任せになっていて、お客さんは踊らされている状態だ。そんな宛がわれたような選択肢では、ただ流行にながされて、他人の真似しかしない日本人の一員になってしまう。
他人と違う方式を試みる精神がこの車両の製作に現れているではないか。 これが完成して走っている姿をみて、どんな乗り味なのか興味を持つ人は多いだろう。しかしその答えは作った者、乗った者にしかわからない領域だ。
無意味だと思う人には一生わからない答えだろう。 そしてこの製作を実現する手段に弊社を選んだ依頼者に満足していただくために腕を振るわなければならない。