■ リペア・難易度A級の修理
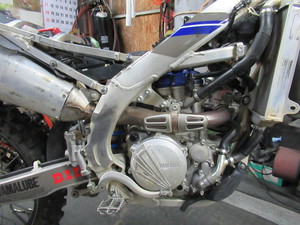
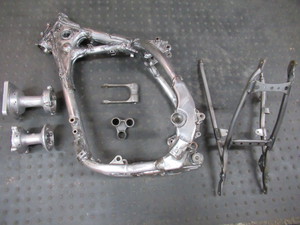
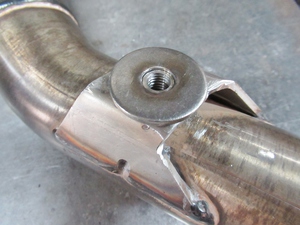
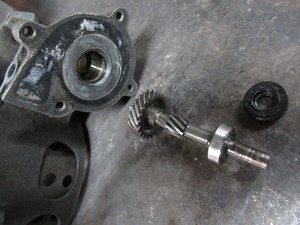
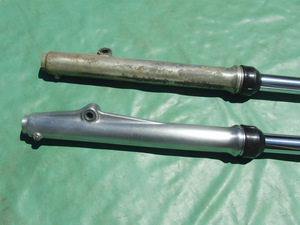
最近のもの忘れの激しさに自分が恐ろしくなります。50歳にしてこの状態では60代で完全にボケてしまうのではないかと思えます。
例えばこんなことがありました。ストーブに火をつけるライターをエアコンに向けてカチカチとスイッチ入れようとしたり、お昼にラーメン食べようと思って包丁でナルトを切って包丁とまな板を洗って、包丁を包丁立てにしまおうとしたらナルトが立っていたり。
または灯油を買いにいこうと思ってポリタンクをスクーターに積んで走りだしたのに、家のそばのGSを通り過ぎて次の交差点まで突っ走って気がついたり。
今、何をやろうとしているか、または1分前の行動が記憶に無かったり、かなり重症のもの忘れです。
そしてついに仕事上のもの忘れで大失敗を犯してしまいました。
このサイレンサー、材料支給で組み立てを頼まれたのですが
完成したつもりで梱包して荷物発送した後で、中に入れ忘れたものに気がついてやり直しするために依頼主に電話して返送してもらったばかりです。
中身のパンチングが後ろに抜けてこないためのストッパーを付け忘れたので、このまま納品したら、お客さんとこで問題が発覚するのではないかと思いました。
早速、溶接を剥離して分解する前に、パンチングを引き抜いておこうとしたのですが、意に反して抜けてきません。
差し込んであるだけなので、バーナーで炙ってアルミを膨らませておけば緩むだろうと思ったのですがビクともしません。
パイプを中に突っ込んで力任せにど突いていたら、アルミの方が負けてしまいました。
結局、改修しなくてもパンチングは抜けてこないということが分かりましたが、これは偶然の産物であり、自分の設計では抜け止めが必要なことに変わりはありません。
この凹んだアルミも修復して無駄にしたりはしません。余計な仕事が増えただけです。
しっかり溶接されたものを再使用できるように分解することは至難の業です。
切断したパイプの部分は寸法が足らなくなりますので廃却して新規に製作です。
やり直しするということは同じもの2回作るより労力が必要です。
往復の運送代も無駄になっていますし、もの忘れの恐ろしさを今更痛感するのであります。
同じ失敗を繰り返さないために、新たに巻いたパンチングにストッパーリングの取り付けを確認しました。
1個品物が増えていますが、追加で頼まれましたので工賃をいただかないで運送代の足しにしていただこうと思います。
あと少しで組み立て完了のところで夜10時を回ってしまいましたので、近所迷惑にならないように、続きは明日の朝ということにします。
翌朝組み立て完了しました。
全損になる可能性もありましたが材料の予備はないので、悪戦苦闘して改修しました。
アルミは柔らかいので溶接を剥がすときに歪んでしまうので、新品で作るより困難です。
私のもの忘れが原因で約束の納期も守れず、余計な運送の手配などしていただき、依頼者の方には大変申し訳なく思っています。
エンジンの組み立てなど、作業が決まっている場合は同じことを2回以上確認して締め忘れや未取り付けを防止できますが、初めてやる作業や方法が確立されていないことはミスが出る可能性が高いことを忘れないで今後の仕事に取り組んでいきたいと存じます。
私らが子供のころはズボンの膝や上着の肘が擦り切れたら、継ぎ当てをして着ていました。着る物や食べる物が貴重で粗末にすると親から怒られたりしました。ですから使える物はなかなか捨てません。可能なかぎり直して使います。
競争原理主義であるはずのモトクロスをやるようになっても貧乏性のままで、チャンバーなどは転倒で簡単につぶれてしまうので、下手な板金修理で直して使い続けました。そんな苦労した経験から、安価に上手く直せればいいなと思って始めたのがチャンバー作りなので、スペシャルパーツとかチューニングとかの目的ではなく、高価な部品をあっさり交換するのでなく直して使うことで出費を抑えようという目的でした。
エクボくらいの凹みですが、これを直してほしいという依頼です。
「金は持っている」といいますが、これが直ったとしても価値があるとは思えませんので、どれほどの難易度か確かめるためにやってみます。
250のエキパイは以前、やりましたので治具がありましたが450のパイプには使えません。
450専用の治具を製作しました。
パイプの端面を密閉して窒素を加圧するための道具です。
エキパイに加工が必要です。
治具が引っかかるストッパーを溶接してあります。
これがないと圧力で治具が動いてガス漏れしてしまうためです。
窒素を10気圧かけてバーナーで赤熱します。
炙りすぎると酸化してチタンが脆くなってしまうので手早くやらねばなりません。
溶接ビードの真上なので、一般部より固かったですね。
凹みはこの程度修復できました。
焼け跡が残りますので色は美しくないですが、凹んでいるよりはいいでしょう。
こっちの方が重症です。
カーボンパイプは衝撃が加わると割れてしまいます。接着剤では再び剥がれてくるでしょう。
これは諦めてアルミで巻いて作るように頼まれましたが、忙しいので後回しにします。
先週末、つまらん仕事に手こずり予定が狂ってしまったので時間を取り戻すために日曜も業務でした。おかげで先週完了予定だったサイレンサーを今朝発送できました。
YZ85サイレンサーですが、ミニモト用商品としては一番多く作ったと思います。
2ストトレール用チャンバーに並ぶ主力商品となっています。
本当は新機種のマフラーを作りたいですが、大きいメーカーが競って新商品を出しますので、零細な個人商店は出る幕がありません。
そこで、どこもやっていない旧式マシンのマフラー作りが回ってくるという寸法です。
暇にならなくてありがたいことです。
削れた部分を切り取り、新しいアルミ板を板金で丸みをつけた後、仮止めします。
気をつけることは、元の板と段差ができると溶接後に修正が効かないので、繋ぎめを同じ高さで止めるということです。
溶接で歪みますので、仮止めは多い方が狂わないでしょう。
繋ぎ目がなるべくわからなく仕上げるところが腕の見せどころですが
あまり上手じゃないですね。
実は新しい物を作るより、部分的に修理して元どおりにする方が困難だったりします。
このエンドカバーは純正部品で¥4000で購入できるので、迷わず新品に交換した方が手間がかからないです。
しかし、私は部品交換屋ではないことを示したいために敢えて板金溶接することを選びました。
削れてしまったサイレンサーボディは5cmカットしてリベット穴を空ければ再使用できます。
インナーパイプも5cmカットして差込部分を溶接します。
2013モデルのサイレンサーは5cmカットしても音量規制をクリアできることを確認してあります。純正品は消耗も考慮して騒音に対して余裕をもった仕様になっているのです。
全長が長いので、転倒でエンドカバーが衝突しないためにも短い方が有利です。
板金修理したエンドカバーに色気を持たせるためにバフ仕上げとしました。
5cmショート化とポリッシュによる輝きでノーマルサイレンサーとは違った外観になるでしょう。
傷ついたから、あっさりと社外マフラーに取り換えるよりも、個性的になるとは思いませんか。
関東選の翌日、オフビレに伊田選手のお店で使うスノースクート用フレームの改修のため、打ち合わせを兼ねてMX練習に行きました。
偶然隣に止めてあったバイクキャリア積載のCRF250のマフラーが酷く削れているのが気になりました。暫くして持ち主が戻ってきたら、昔のミニモトライバルでした。彼の乗っていたCR125のチャンバーやアフリカツインのマフラーも作ったことがあったので思い出しました。
問題なく乗り回していましたが、「これはどうした?」と尋ねたら
関越道でキャリアから落として引きずった、と言います。
タイダウンが引っかかっていたので、後続車に衝突されることは無かったのが不幸中の幸いです。
ハンドルもメチャメチャになったので取り換えましたが、マフラーは中身にダメージがないので走行に支障ありません。カッコ悪いだけです。
部品交換で治せばよかろうと思いますが部品代はマフラーボディ単品で¥42700もします。リベットも20箇所で¥1600します。交換工賃¥5000でやったとしても5万円オーバーですから悩むところです。
修理代5万円出すなら、社外のマフラーに取り換えてしまうところです。このマフラーは純正で¥88000もするのに驚きです。お金持ちでないと、なかなか取り換えないでしょうね。
しかし、彼は東京ドームの近くで飲食店を経営していて今度2店舗めを出す予定の実業家ですから新品交換などわけないことだと思います。しかもお気に入りの国際A級ライダーに現金スポンサーもしているそうです。
その彼が私に「どうすればいいですか?」と聞くので
ダメなとこだけ作って取り換えればいいんだ、という具合にいつものように安易に答えてしまった責任をとるために、練習後マフラー外してお持ち帰りすることになりました。
修理代大幅削減は確実ですが、これにかかっていると仕事の予定に影響がでますので、納期はゆっくりでいいという確認をとって、再来週くらいに治したいと思います。
彼と彼の奥さんはスノースクートにはまりつつあるのですが、マイスクートを持っておらず、今度伊田選手のお店へ行く約束をしていましたので、スクート2台買っちゃいそうなので、伊田選手もうすぐ儲かりますね。
仕事というものは一人だけでは成り立ちません。需要と供給、そして自分の持ってないものを補ってくれる人脈が大事という一例でした。
チャンバーの凹みがどの様に直っていくか、実態がわからないためか質問を受けることがあります。そこで調度よい修理依頼が来ましたので掲載してみます。
機種はRMX250Sで半年ほど前に販売したものです。
転倒したらしく大きく凹んでいます。
真横から見ると酷い状態がわかりますね。
修理方法は棒を溶接して引っ張るとか、裏側に穴を開けて棒で突くとか、おっしゃる人がいますが、仕上がりを想像すると恐ろしいですね。
空気圧をかけてガスバーナーで炙る人もいますが、鉄板が酸化してしまって外観も強度も落ちてしまいます。
この程度の凹みなら水圧方式が簡単でしょう。
口元とテールパイプに治具を取り付け水押しの準備は整いました。
この角度が変形の入り具合がわかりやすいですね。
それでは圧力をかけていきます。
圧力は物と状態によって調節しますが、この場合は35気圧かけています。
圧力だけでこの程度戻りますが、これから板金ハンマーを使って形状を整えていきます。
およそ10分ほどハンマーで叩いて均していきます。
方法は高い所を叩くと水圧がバックアップになって低い部分を押し上げてきて同じ高さになります。
路面の固い所に当たったのでしょう。傷が沢山見えますが、これはこのままにします。
サンダーで研磨すれば傷は目立たなくなりますが、板厚が薄くなってしまうのでこのままのほうが強度が保てます。
これくらいの修理なら2回、3回と繰り返しても再使用できます。
跳ね石で小さい凹みができていますが、実は大きい凹みより直りにくいことがあります。
それは固いものが食い込んで鉄板が伸びてしまっていることと、水圧を受ける面積が小さいのでバックアップされる荷重が低くなることが要因です。
しかし、大体痕がわからない程度に直りました。
棒を溶接して引っ張っていたらこのように仕上がらないはずです。
但しこの方法で直せるのは、断面が真円のパイプに限ります。楕円パイプなどは、圧力で真円になろうとしますので形状が変わってしまいます。そういうパイプは面倒ですが切開板金するしかないでしょう。
最後に治具に取り付けて歪みの確認をします。歪みが大きいと車体に取り付かなくなることもありますので矯正が必要です。
これはラインナップ品なので、これが可能ですが、社外品は形状が違っていて治具に取り付かないので、歪みの確認ができません。
その場合は車体合わせで確認する方法を採ります。
バックオーダーは1ヶ月分残っていますので、社外品マフラーの修理は優先的にはできません。2ヶ月以上お待ちいただいているお客さんの注文がありますので順番に進めております。
不運にもマフラー壊してしまった場合は、新しいものに交換されることをお勧めします。
また実車は殆どありませんので取り付け確認などが必要なほど変形している場合も保証できないことをご了承いただきたいと思います。
カーボン樹脂製のエンドキャップが割れてしまって交換が必要ですが
補修パーツもありませんので、鉄板で作って代用します。
ビレットパーツのマウントステーですがリベットが外から外せない構造でしたので、ボディーを切って内側のフランジを削除して外しました。
マウントステーの面積が小さいので加重を受けるとボディーに食い込んでしまう難点があるようです。
チタン材は非常に高額になりますので、アルミ板でボディーを作って代用します。
修理というより半分製作という形になります。
メーカーから補修パーツが販売されることが理想だと思います。
マウントステーの取り付け位置は全く不明なので実車をお借りしてマーキングしてから取り付けることにしました。
今回は隣の川越市在住の国際A級ライダー松本耕太選手のガレージにお邪魔してきました。
彼はお父さんの会社で働いているのでお給料でチャド・リードと同仕様の前後サスペンションを購入してCRF450Rに奢っています。モトクロスは気が向いたときだけ乗るというお気楽モードが信条のようです。レース出てもお金になりませんからね。
私は言い訳をしなければなりません。これで許されることとは思っていませんが、競技者、製造者、顧客などの立場を考慮した結果このような処置をとることにしました。
マフラーの製作依頼を受けて順番に作業を進めていますが、手作業のため2ヶ月程度お待ちいただいている状況ですが、突発で頼まれる依頼に対応しなければなりません。
レース中のアクシデントでマフラーとサブフレームが曲がってしまい、タイヤがマフラーに擦りながら走行した結果このようになりました。
折れ曲がったジョイントパイプ、切れたバンド、エンドキャップ割れ、が損傷箇所です。
パーツを取り寄せて交換したらどうか?と言いましても高価で買えないと言います。
しかし、スペアの新品マフラーは来るということなので、これに金を掛ける気は無いということです。
それならば、金が掛からないように修理方法を考えなくてはなりません。金は掛けませんが、時間は丸一日掛かっていますので、その分お待ちいただいているお客さんの仕事が遅れるということです。時々、突発の仕事が入りますので作成した工程表の通りに予定が運ばないことが言い訳の内容です。
ここが折れ曲がったジョイントパイプ部分ですが画像は炙り戻した後です。若干のシワが残っていますが、マフラーの向きは正常に修復できました。
曲がったサブフレームも正常な位置に戻して取り付け状態を回復しておきます。
割れたエンドキャップはプラスチック製です。
このパーツは単品で購入できないそうで、マフラーASSYで8万円掛かるということで迷わず製作です。
コストを抑えるため鉄板で板金製作です。
仕上げはつや消しブラック耐熱塗装です。
擦り切れたカーボンバンドは単品購入できるらしいですが1万2千円掛かります。
ここもアルミステーとステンレスバンドを作って代用です。気に入らなかったら部品発注してください。
オリジナルを見たことが無い人は改造したことが分らないでしょう。
レストア界の最高権威、小林さんから溶接肉盛りを頼まれたケースカバー。
左ケースと思いますが、車種が分らない私が質問しましたら、ホンダSAだとおっしゃいました。1955年製の同車種ですが、最近まで実動で、イタリアで開催された2000kmのラリーを完走して年代別クラスで入賞したマシンだそうです。
ヨーロッパの旧車レースは日本とは比較にならない人気とレベルの高さが予想されます。
自分を育ててもらった会社のマシンですから、恥ずかしながら調べてみましたら、これがホンダの2輪車の歴史上重要な役割を担ったマシンであることがわかりました。
ホンダコレクションホールの展示車画像から拝借しました。
たしかにこの車両の左ケースが同じ形状を呈しています。
これがホンダ初の4ストエンジン、OHC単気筒250ccです。
本田宗一郎さん直々の設計で、夢の4ストロークエンジンが完成したので、ドリームという車名を与えた最初のマシンです。
製造された1955年にレースに出場しています。日本にサーキットが無かった時代で
7月に第3回富士登山レースで250ccクラス優勝。11月の第1回浅間火山レースで250ccクラス2位入賞という快挙。因みにこのレースの優勝はライラックに乗る伝説のレーサー伊藤史郎でした。
修理内容は、オイルドレンに亀裂が発生したため溶接肉盛りをすることです。
古いダイキャストですから表面を少し削って地金を出す必要があります。
酸化皮膜が溶接不良を引き起こすためです。アルミの溶接は交流TIGを使いますが、交流は極性が+ー交互に流れる高周波です。+イオンを衝突させ酸化皮膜を除去しながらー電子でアルミを溶かします。この酸化皮膜が強固な場合、除去できずに上手く溶けてくれないため、予め削っておくことが必要です。
内側もこの通り一皮剥いて、浸み込んだオイルの脱脂も行います。
ネジ穴の内側から溶かすように溶接棒で埋めてしまいます。
ここに新たなネジ穴とボルト座面を加工するのですが、私の仕事はここまで
続きは小林さんのレストア工房の加工機で行います。
サンドブラストで全体を美しく仕上げて、消耗部品も新品交換して組み上げますので、新車同様のコンディションになるでしょう。
小林さんは、ホンダのワークスレーサー、ダブルプロリンクや2気筒RCなどの開発を勤め、オートマチックRC時代のHRC監督でしたが、その後、会社命令でコレクションホールの立ち上げを任され、茂木の展示車両は同氏の作品であります。
英国バーミンガムのモーターサイクルミュージアムも見た事がありますが、展示台数は多いですが、旧車のコンディションは悪かったと思います。それに比べて、茂木のコレクションホールは全車動態保存で外観も新車同様、F1やMotoGPの歴代チャンピオンマシンも保有していることで、間違いなく世界一の2輪4輪博物館であると同時にホンダの偉業を実物で感じ取れる、後世に伝えたい異空間であることを申し上げておきます。
CRF250 10モデルのマフラーですが、インナーパイプのエンドキャップ部分で破損してパンチングパイプが中で外れてしまいます。
レーサーですから補償はありません。しかし、寿命の設定としては絶妙ですね。
去年のモデルですから1年間壊れなければクレームもつかないでしょう。壊れれば部品交換しなければ走れませんので、やむを得ず交換するのですが、この部品だけで2万円以上しますから、分解工賃など加えると3万円くらいの出費でしょう。
画像はエンドキャップを修復した後です。破損したキャップ部分に鉄板を追加して補強していますので寿命は大幅に伸びるでしょう。
分りにくいですが、エンドキャップの内側にエンドパイプを差し込むツバがあったのですが、パイプが中で暴れて無くなっていたので、ツバの部分も修復してあります。
溶接場所はこのとおり、これで僅かな材料で元どおりの機能を果たすことができます。
修理代も純正部品で交換するより大幅に削減できました。
社外品のマフラーは修理しません。他店でお買い上げいただいた商品については、他店に依頼してもらいたいからです。
純正部品を修復してスペアマフラーにしながら我社の製品をお買い求めのお客さんに対するサービスとして安価にて提供するものであります。
エキパイの凹み、熱影響のためか外側が延びて潰れたように変形しています。
曲げるときは、パイプの断面積がなるべく変わらないように注意して作りますが、激しく走行しているうちにダメージを受けてしまいます。
こういう状態のエキパイを修理するのに、チャンバーのように蓋をして圧力を掛けようとしても元通りにはなりません。
スッキリ直すためにダメージを受けた部分を取り換えます。
メーカーによって特殊なサイズのパイプを使用している場合があり、パイプが入手困難で修理断念していただくこともありますが、
これはφ31.8でパイプの在庫がありましたので、直ぐに曲げました。
パイプベンダーという高価な設備はありません。万力とバーナーを使って手曲げによるものですが、内側40Rで潰れないように180°曲げて素材を作ります。
パイプのサイズが大きくなるにつれて曲げられる最小Rが大きくなっていきますので、車種によっては難しいものもあるでしょう。
潰れたパイプは切除して新しいものに取り換えて溶接しました。
チタンパイプは材料代が高価で3万円くらい材料購入してエキパイ3台分が作れる程度です。
ダメージの無い部分を再使用することで、新品の半分以下のコストで修理することが可能となります。
勿論、予算に余裕がある人は新品購入された方が経済の活性化に繋がると思いますが、修理代を節約して、もっと有効なことにお金を使うことができるということです。
2ストトレールは健在です。これは公道バージョン、オンロードタイヤでフロントインチダウンされています。
外装も丁寧にカスタムされていて、大事に乗られていることが分りますが
94モデルなので登録から17年経過していて、走行距離は5万キロくらいだそうです。
さすがに、このまま乗り続けるのは不安だということでエンジンOHすることになりました。
社外のチャンバーも激しく凹んでいます。これはオーナーがヤフオクで凹んだ状態のものを安く落札したそうですが、普通は社外品の修理はお引き受けしません。それは、マフラーメーカーか販売店が対応すべき仕事だと考えていますので、私が社外品を使い続けるために救済する必要は無いと思っているからです。
トヨタの販売店にホンダ車の修理を頼むようなものですからね。そうは言っても、こちらのお客さんが、この車両を総合的に直したいと依頼してこられているわけですから、その一環としてチャンバーの修理も行います。
リヤショックはオイル漏れの上、バンプラバーもウレタンが崩れて無くなっています。ショックもOHして機能回復しなければなりません。
チャンバーはエキパイ部分から全体に潰れていて、まともな状態ではありません。ここまで潰れていると商品価値はゼロだと思うのですが、ヤフオクではこのようなものに5千円の値段をつける人がいるそうです。明らかにスクラップであることを付け加えておきます。
オイル漏れの激しいエンジン。シリンダーベースにコーキングが見られますが、ガスケットが吹き抜けていることが予想されます。
さすがに5万キロのダメージが蓄積されているのでしょう。
これから全バラして修復することにします。
排気デバイス、KIPSの部品です。
遠心ガバナーにより駆動される可変ポートタイミング機構です。ラック&ピニオンで中央のスライドバルブと左右の回転式バルブが低速域と高速域の排気ポートタイミングを変化させて、幅広いパワーバンドを稼ぎ出します。
しかし、その部品点数の多さは4ストロークエンジンの動弁系より多く感じられ、メンテナンスの工数も、こちらの方が上です。
エンジン部品全部。ばらすだけでなく、相当な汚れが付着しているので、全部洗浄してからメンテナンスに入るので非常に時間がかかります。
汚れが付着していると、小さい傷や磨耗の状態が判断できませんので、整備の方針を決めていく上で重要な工程です。
こうして、交換部品のリストアップが可能になります。
従って正確な見積もりはこの段階以降でないと分りません。
エンジン整備には夏でも石油ストーブを使います。
ベアリングの交換にはケースを熱膨張させて、脱着します。これはケースにダメージを与えない方法で
プレス機を使った圧入では圧入面がかじって、小さい傷がつきます。そのため折角、真円に加工された穴やベアリングが偏芯してしまうので、それを防止します。
2010モデルから著しく大型化したCRFのサイレンサーですが、思わぬ不具合も生じています。
張り出したサイレンサーは転倒しなくても、通常のライディングでサイドカバー越しに圧迫されてデフォーム(凹み)が発生します。また角ばった断面のアルミは平面が広くなっていますが、排気圧で膨らもうとしますので、金属疲労により亀裂が入ってしまいます。
上は2011CRF250R、下は2010CRF450R。
250方が450よりサイレンサーが大きいことが分ります。
これらのサイレンサーは純正部品で一個9万円もしますので安々と買い換えられるものではないでしょう。
レーサーモデルも高品質化して付加価値を付けていかないと商品として受け入れてもらえなくなるということは予想できますが、限度というものがあります。
私が自分の150用のマフラーを作る理由はクラッシュで一発破壊する恐れのあるものが、純正部品で5万円もするので、作る場合は半額程度のコストで済むからです。
この高いマフラーの仕様を設定する人たちは、元々高収入で中小企業の社員とは違います。その上、このようなレーサーモデルは会社の車両に乗れるため、自分で買う必要がないですから、一般庶民の金銭感覚は持ち合わせていないのではないかと思ってしまいます。
これはどちらも国際A級ライダーが所有しているものですが、日本ではトップクラスの彼らでさえ、スペアサイレンサーを持っていないという現状からも、その問題点が感じとれます。
とりあえず、修理するためにはリベットをはずして分解しなければなりません。
現在バックオーダーの状況が2ヶ月分溜まっているため、新規の注文を先延ばしするか諦めていただくなどの対応をさせていただいている状態なので、作業する時間がとれるかどうかわかりませんが、修理してみることにしました。
まずは450から
アルミ筒に絞りが入っているため
切断して別々に整形してから溶接です。
大体、元の形状に直りました。
次は250です。
デフォームを均してから亀裂部分を再溶接です。
古い溶接ビードを削除して溶け込ませていきます。
ビードは平滑でないと、すぐに割れてしまいます。このあと外側にアルミ板を張り付けツインウォールにしますが
これは国際A級用なのでスペシャル仕様の加工を行います。
音量に余裕があることと、加速力を増す目的でショートタイプに変更。
テーパーパンチングのため繋ぎめの外径を合わせて溶接しています。
アルミ筒はデフォームになりやすい外側をツインウォールにしています。
エンドキャップの嵌め合いがきつくて、経験のない人は組み立てが難しいと思います。
グラスウール詰めて、ステンリベットで荷締めて組み立て完了です。
高価なマフラーなので、メンテナンスして寿命を延ばしてあげないと、亀裂が拡大して使用不能となって
余計な出費が出ますからね。
・・・ああ、また予定が遅れてしまった・・・
今週は休みなしで働きます。
「これ直すんですか?」一応確認のため聞いてみた。そしたら「直したい」という答え。
「ものすごく大変だよ」と言うと、「いくらぐらいですか?」というので「普通の3倍くらいかかるよ」
と答えたら、「新品買った方が安いですか?」と言うので、「そこまではいかない」ということで
契約成立して修理することになった。
普通はこのように大破している場合は新品に交換するように勧めます。
それは修理に相当な時間を費やし、製作業務に差し支えるからです。
おそらく、これは、新品交換した上で直したチャンバーはスペアとして取っておこうということだと思います。
そして、直らなければ諦めると思うのですがダメ元で聞いてみるということは、私が直せるかどうか試しているのではないかと、思わせるのです。
これが直ったとしても私の評価が上がるわけでは無いと思いますが、もしかして直せないんじゃないかと思われることが、マイナス要素なので
この挑戦に応えることにしました。
ここが荷重の力点だと推測しますが、鉄板が破けています。
圧力をかけて直すために、溶接して穴を塞ぐ必要があります。
エキパイにシワがよって蛇腹のように曲がっています。
ここまでいくと、水圧では直りませんので
切断して鉄棒を当てがいながらハンマーで板金修理しなければなりません。
夜は騒音の出る作業は近所迷惑になりますので、この続きは明日ということにします。
パイプを切断し、潰れた部分をハンマーで整形して溶接。
その後、水圧で元の形状まで膨らましました。
しかし、そのままでは歪みが大きく車体に取り付けができないくらいパイプの向きが変わってしまいました。
結局、4箇所の切断面を削ってパイプの向き矯正して取り付くようにしました。
MTBプロライダー、日本人として始めて海外メーカーと契約し世界選手権を走った世界ランカー。
アジア選手権2連覇、JCFシリーズチャンピオンなど輝かしい戦績をもつダウンヒルライダー
井出川直樹選手はホンダレーシングとも契約してRN01で戦ったこともある。
現在、彼は京都のダイアテックと契約し、カナダのEVIL(イービル)というメーカーの自転車に乗っている。
しかし、このEVILは国内に1台しか輸入されておらず、
即ち井出川選手専用のプロトタイプでスペアマシンもない。
これが、EVIL社スイングアーム、部品単価は聞いてないが、メインフレームだけで40万円くらいだそうだ。
これをハンドワークで1品だけ製作頼まれても、この前のスイングアームより3倍くらい手間が掛かりそうだ。大体、切削部品をこのクオリティで仕上げるにはNC(数値制御)マシンに頼るしかないわけだが、NC加工の工賃は段取り1回の金額なので1個加工するのと50個加工するのとあまり変わらないので、1個だけ加工すると莫大な金額になってしまうので普通はやらない仕事だ。
幸いこれは2箇所のヘアクラックを補修するだけなので問題はない。
クラック2箇所、塗装を剥離してからTIG溶接することになる。
亀裂を溶接だけでは再び発生してしまうだろう。
再発防止のために補強パッチを追加しておく、これで寿命は格段に向上するはずだ。
こちらはビード肉盛りで様子をみる。
このスイングアームは左右非対称な接合方法で、こちら側だけ突き合わせになっていることが
強度不足の原因とおもわれる。
高負荷の足回り部品を溶接する場合、荷重の方向に対してなるべく長手方向に接合することが
セオリーなのであるが、突き合わせが最も不利な条件なのである。
いずれにしても日本屈指のダウンヒルレーサーが溶接修理を頼ってきてくださったことに感謝いたしまする。
2スト車の車体に4ストエンジンのスワッピング(換装)は何度もやってきた。 しかし今回のスワッピングは今までのとはわけが違う。
これまでのエンジンは旧式の空冷2バルブであったのに対し、これは新型の水冷4バルブだ。 おそらく日本で初めての組み合わせだろう。前後サスペンションはホワイトパワー。リヤはリンクレス。 ブレーキはフォーミュラの対向ピストン。国産には採用されないヨーロッパ製品が目を引く。 画像はエンジンのレイアウトを検討している様子でエンジン位置は決定したがフレームのパイプは繋がっていない。高くなったキャブレターにあわせたエアクリーナーの変更、シリンダーヘッドをかわしたガソリンタンク製作、フレーム中通しの専用エキゾーストパイプetc.難題山積みである。 おそらく実走できるのは夏頃だろう。
この製作計画を聞いて殆どの人は無意味だとか、改造しないでそのまま乗るのが一番いいとか思われるだろう。 実は製作を担当している自分自身も同様に思っていたのだが、製作を諦めさせる説得をしながら、自分の気持ちが完成させて走らせてみたい方向に変化していった。
これを無意味なことと思う人は、マシン選びにどれ程の理由があるだろう。 メーカーのイメージであったりレースで上位を走る機種であったり、バイク店との付き合いであったり。いずれにしても明確な根拠は存在しないはずである。しかも、高額な支払いをして手に入れたマシーンも翌年にはあっさりモデルチェンジされて旧式になってしまう。本当に乗りたいものを決める手段が完全にメーカー任せになっていて、お客さんは踊らされている状態だ。そんな宛がわれたような選択肢では、ただ流行にながされて、他人の真似しかしない日本人の一員になってしまう。
他人と違う方式を試みる精神がこの車両の製作に現れているではないか。 これが完成して走っている姿をみて、どんな乗り味なのか興味を持つ人は多いだろう。しかしその答えは作った者、乗った者にしかわからない領域だ。
無意味だと思う人には一生わからない答えだろう。 そしてこの製作を実現する手段に弊社を選んだ依頼者に満足していただくために腕を振るわなければならない。
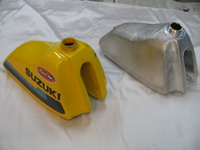
